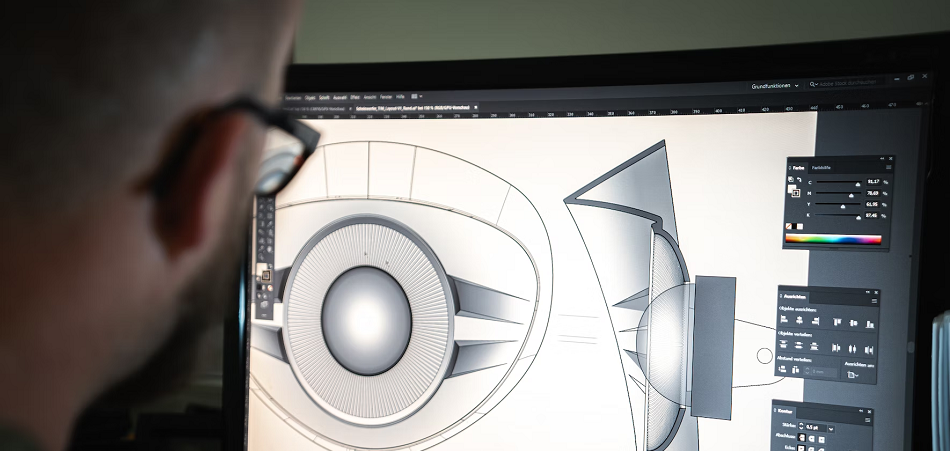
The first computers used for structural analysis were analog machines that solved series of differential equations. These early machines were built starting in the late 1930s and were mechanical in nature using springs, gears and other devices. One of the more significant such devices was the machine built by John Wilbur, a professor of civil engineering at MIT, which is shown in Figure 22.1. During the late 1940s and throughout the 1950s electronic analog computers were increasingly used to solve mechanical analysis problems, particularly in the aerospace industry. Most of these computers had difficulty solving problems with more than 200 degrees of freedom.
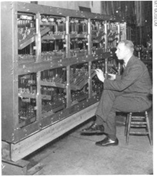
Even with this limitation, significant stress and vibration problems were successfully handled. According to Richard MacNeal, the founder of MacNeal Schwendler Corporation (known today as MSC.Software), Sud Aircraft in Paris built an analog computer that was capable of handling the analysis of the wing structure for the Concorde supersonic airplane, a problem involving 2,000 degrees of freedom. This was probably the upper limit for analog computers. Something better was obviously needed. That something turned out to be a technique we know today as Finite Element Analysis or FEA. This approach involves dividing an object such as a mechanical part or a building structure into small elements and then using the mathematical relationships between these element to compute stresses and deflections caused by various loading conditions. FEA technology evolved as an academic concept in the 1950s and soon caught the attention of structural analysts in the aerospace industry and at NASA. For the most part this chapter focuses on companies that specialized in the development and marketing of software associated with finite element analysis (FEA).
The software used to create sets of elements is usually referred to as finite element modeling (FEM). The term frequently used to describe this data was a finite element mesh and the software was also called a mesh generator. Another way of describing the complexity of an analysis problem is by stating the number of degrees of freedom the structure has. This is usually some multiple of the number of elements. Models are also referred to in terns of the number of nodes – the vertexes where two or more elements meet.
One of the first papers on this subject was published in 1956 in the Journal of Aeronautical Engineering by a group of Boeing engineers led by Jonathan Turner.[1] Another early pioneer in this area was Raymond Clough, a professor of mechanical engineering at the University of California at Berkeley who published a paper, “The Finite Element Method in Plane Stress Analysis” at an ASCE conference in 1960.[2] As described below, several others were experimenting with this new analysis technique at the same time.
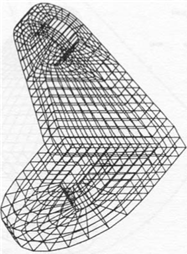
The nature of FEA has changed significantly over the years. Early software was implemented on batch-oriented mainframe computers. The process most commonly used for building FEA models prior to the introduction of computer graphics involved taking drawings of the object to be analyzed, laying out a grid on these drawings and then manually dividing the object into discrete elements. Since the accuracy of the results often depended upon the number of elements in the model, analysts tried to split up the part as finely as possible given limitations of time and budget. They had to keep in mind that the time to compute a solution went up geometrically with the number of elements in the model. The entire process for an initial analysis of a part with 1,000 elements would have taken several weeks. Subsequent analyses typically took several days.
Each element was entered on a coding sheet, the sheets were given to a key punch operator and entered into punch cards and the data on these cards was printed so the engineers could check for obvious errors. Small numerical errors were difficult to find as were missing elements or missing information defining how each element was connected to adjacent elements. These points of connection are referred to as nodes. Only after the data was thoroughly checked by hand could it be run through a FEA program and the results printed out. Some, but not many, organizations used plotters to create drawings of the FEA input data or to illustrate results. More often, results were reviewed by going through page after page of numerical listings and plotting this information by hand.
The process was excruciatingly tedious, susceptible to error and costly. Even moderate size problems required a large amount of time on fairly large computers. Slight errors in preparing the data often made these expensive computer runs worthless. If FEA were to fulfill its promise, the process needed improvements from end to end. A number of companies started to envision the use of interactive graphics as a means of improving this process.
By the mid 1970s, computer graphic systems were starting to be used to prepare FEA data and to view results. For example, McDonnell-Douglas Automation offered a timesharing program called FASTDRAW that could be used to create element data and then transfer the information to a mainframe analysis program. SDRC was another company offering this type of software as described in Chapter 17. At the time, most analysis work was done by highly educated engineers and mathematicians, often with Ph.Ds.
A decade later most CAD vendors offered programs that would take a threedimensional model and generate FEA input data with minimal user intervention. With greater automation of the mesh generation process, models became larger and larger. It was not unusual for a large model to consist of 100,000 elements and there were a growing number of element types being used. Some of these were fairly complex in order to solve problems such as those involving thin shell structures. With the computers of the early 1990s, a large problem could still take several days to solve, even on a supercomputer. One result was an increased focus on developing new mathematical procedures that would enable analysts to economically solve larger and larger problems.
Today, large models can consist of several million elements yet are solved in relatively short order on desktop computers. One major change is that FEA software is typically used interactively by design engineers now as well as by analysis professionals. If an engineer is trying to reduce the weight of a part, software is readily available that will optimize the shape of the part. In some industries, FEA simulation has eliminated most, if not all, physical prototype stages. Today, crash analysis in the automobile industry is primarily done using FEA rather than building physical prototypes and smashing them into a wall.
The March 1992 issue of Computer Aided Design Report listed 28 different companies that offered finite element analysis software.[4] Some of these, including Computervision and Intergraph, are discussed in separate chapters while others are discussed in this chapter. Space constraints do not permit covering every company, however.
ABAQUS (Hibbitt, Karlsson & Sorensen)
The early history of ABAQUS is very tightly connected with the early history of MARC Analysis Research Corporation described later in this chapter. Both companies evolved out of work done at Brown University in Providence, Rhode Island starting around 1965. David Hibbitt received his Ph.D. in 1972 from Brown after completing a thesis involving computational mechanics using the FEA method. Hibbitt was hired by MARC Analysis Research Corporation where the code developed as part of the thesis formed the basis for the initial MARC software. Paul Sorensen also worked briefly for MARC before returning to Brown to complete his Ph.D.
Throughout the 1970s and into the 1980s, MARC was provided to users on a time-sharing basis, particularly via Control Data Corporation’s Cybernet service. Dr. Bengt Karlsson worked for CDC in Sweden supporting a number of different analysis programs. In 1976 he moved to the United States and also joined MARC.
A year later, Hibbitt decided to form a new company to develop and market FEA software that could be used by a broad range of engineers. This software was called ABAQUS. Karlsson joined him in the effort as did Sorensen who was working at General Motors. The three incorporated Hibbitt, Karlsson & Sorensen or HKS as it was most commonly known, in February 1978.
Like MARC, ABAQUS was initially distributed via CDC’s Cybernet service. The company’s first customer was Westinghouse Hanford Company which used the software to analyze nuclear fuel rod assemblies. Over the years ABAQUS developed a following among engineers working on complex projects such as offshore oil and gas platforms as well as in the automotive industry for vehicle simulation. The company developed a reputation of working closely with ABAQUS users in deciding where to concentrate its development resources.
The basic software, eventually known as ABAQUS/Standard, was complemented by other software tools including ABAQUS/Explicit, a dynamic analysis package released in 1991, and ABAQUS/CAE, a package for building FEA models from CAD data released in 1999. The company’s name was changed to ABAQUS, Inc. in late 2002 to reflect the company’s focus on this product line. Then in October 2005, the company with its 525 employees was acquired by Dassault Systèmes for $413 million or about four times the company’s annual revenue of approximately $100 million.
David Hibbitt was still with the firm he started as chairman while Mark Goldstein was president and CEO when the company was acquired by Dassault.
ANSYS (Swanson Analysis Systems)
John Swanson joined Westinghouse Astronuclear Laboratory in Pittsburgh in 1963 as manager of structural analysis. While working for Westinghouse he completed his work on a Ph.D at the University of Pittsburgh in applied mechanics in 1966. He had earlier received his bachelors and masters degrees in mechanical engineering from Cornell University. While at Westinghouse, Swanson promoted the use of computer models to predict the stresses and displacements of nuclear reactors due to thermal and pressure loads.
Recognizing the future potential for this analysis technology, he recommended that Westinghouse begin the development of general purpose FEA software. When the company turned him down he decided to start his own company, Swanson Analysis System, in 1970. The first version of what soon became the company’s flagship product, ANSYS, was developed using a time-shared mainframe at U.S. Steel. The initial version of the software was finished by late 1970 and Swanson’s first customer was Westinghouse.
While ANSYS initially was implemented on mainframe and supercomputers, Swanson was an early supporter of the new generation of 32-bit minicomputers such as the Digital VAX 11/780 which was quickly becoming popular in engineering and academic circles. The company also recognized the need for both model preparation and results viewing software. Its popular Finite Element Modeling (FEM) package was called PREP7 while its viewing program was POST1. The use of all three provided a well integrated FEA solution.
Over the next decade, the company gradually built its market presence, becoming a well respected vendor of technical software although not a very large one. The company expanded into the area of computational fluid dynamics when it acquired Compuflo, Inc., the developer of FLOTRAN software, in 1992. In early 1994, TA Associates, a Boston, Massachusetts-based investment firm, acquired a majority interest in Swanson Analysis. One result of this deal was that John Swanson relinquished his position as president and CEO and for the next five years acted in the role of chief technologist. He was replaced by Peter Smith, an ex-Digital Equipment Corporation executive who soon changed the company’s name to ANSYS, Inc. Swanson was still a major stockholder in the company and remained on the company’s board of directors until early 2000.
By late 1994, the company was focused on several technical objectives. ANSYS Designer Series was being promoted as being design engineer friendly so that many problems could be addressed without the need to utilize analysis specialists. ANSYS 5.1 was also being used increasingly for design optimization. The software supported over 100 different element types and was capable of solving static and dynamic problems, including linear and nonlinear cases. Adaptive meshing automatically adjusted the size of the finite element mesh until the solution converged. Previously, this was a time consuming task for the engineer.
ANSYS 5.1 also including new solution technology that processed FEA models as much as an order of magnitude faster than earlier version although two to four times faster was more typical. Performance was becoming increasingly important as models with over 100,000 elements were increasingly common. This was an area where John Swanson spent a considerable portion of his time once he was no longer president. Significant performance enhancements were periodically incorporated into subsequent software releases. In particular, ANSYS was a leader in applying multiprocessing techniques to FEA computation. Today, ANSYS is regularly used to solve models with well over a million elements.
ANSYS was also working closely with CAD software vendors including PTC and Autodesk to integrate its software with a variety of CAD packages. Its ANSYS/AutoFEA package, introduced in October, 1994, was tightly integrated with AutoCAD Release 12 and sold for just $1,200. A more advanced version, ANSYS/AutoFEA 3D was released in June 1996 at a suggested price of $3,800.
The company was recognized as a leader in the area of multiphysics problem solving. This refers to situations where an analyst addresses problems involving the combination of structural, thermal, electromagnetic and vibration forces. In June 1996, the company had an initial public offering, selling 3,580,000 shares of stock for $13 per share and raising over $46 million for the company. Shortly thereafter, the company’s 300 employees moved into a new facility in Canonsburg, Pennsylvania, 15 miles southwest of Pittsburgh.
During the period from 1995 through 1999 the company’s business model changed significantly. While overall revenues rose from $39.6 million to $63.2 million, software lease revenues dropped from $18.1 million to $16.6 million. Meanwhile service revenue more than tripled from $7.0 million to $22.2 million and the sale of fully paid up licenses nearly doubled from $14.5 million to $24.4 million.
Jim Cashman, became president ANSYS in April1999 and CEO in February 2000. He had joined the company as vice president of operations in 1997 after working for PAR Technology Corporation, Metaphase, and SDRC. He replaced Smith who remained as the company’s chairman. In February 2003, ANSYS acquired CFX, a computational fluid dynamics software company for $21.7 million.
In February 2001, Brad Morley, the former CEO of Applicon, joined the ANSYS board of directors. The company has done well in recent years with revenue in 2005 exceeding $155 million. In May 2006, ANSYS completed the acquisition of Fluent, a vendor of Computational Fluid Dynamics (CFD) software for $565 million in stock and cash. The result was a company with approximately 1,350 employees with consolidated revenues of nearly $264 million in 2006.
Computer Aided Design Software, Inc (CADSI)
Computer Aided Design Software, Inc (CADSI) began as a result of work done by Edward Haug, a professor of mechanical engineering at the University of Iowa. Around 1980, engineers at the U.S. Army Tank and Automotive Command (TACOM) in Detroit, Michigan were interested in improving the mathematical algorithms and formulations used to solve equations of motion for constrained multibody mechanical systems. This led to TACOM funded research at the University of Iowa for computer simulation of vehicle dynamics. Professor Haug and his associates delivered this software to the army around 1982.
Initial tests of the software proved the numerical accuracy of the Dynamic Analysis and Design System (DADS) algorithms and the software quickly evolved to handle a wide variety of truck and tank simulations. Prior to DADS, all software packages tested by TACOM failed to provide the necessary numerical stability, accuracy, and reliability. In 1983 Haug decided to form a company based on this dynamics technology and started CADSI in Oakdale, Iowa to develop software products and provide consulting services in this area. The company’s primary competitor was Mechanical Dynamics which is discussed below.
By 1985 Haug decided he had more interest in being a professor than a businessman so he recruited Rex Smith, a vice president of R&D at Applicon to become CADSI’s president and CEO. Smith had earlier held a similar position at SDRC. The first commercial version of DADS was released to customers in 1986. DADS was one of the first motion analysis packages to incorporate a graphics pre- and post-processor. This software ran on a wide range of computer platforms including PCs and UNIX workstations. In 1989 the software was priced at $27,000. Working with Boeing, CADSI also developed a version of DADS that was integrated with Dassault Systèmes CATIA called CATDADS. Other interfaces were soon developed for SDRC’s I-DEAS and PTC’s Pro/ENGINEER.
In mid-1994 IBM licensed CADSI to sell PolyFEM, a linear structural analysis packaged developed by IBM’s Almaden Research Laboratory in San Jose, California. This software was initially written to work with CATIA. In 1996 IBM had discussions with several companies about selling the PolyFEM technology outright. CADSI was the successful bidder although it had to raise outside funding to finance the purchase. CADSI had hoped to sell PolyFEM to Pro/ENGINEER users who were already using DADS but PTC’s acquisition of Rasna (see Chapter 16) made this rather difficult.
CADSI did put together a combination of DADS and PolyFEM with an interface to SolidWorks called DesignWorks. CADSI was the only company at the time that offered a software product that combined motion analysis with structural analysis.[5] In early 1999, CADSI was acquired by LMS International, based Leuven, Belgium. Various versions of DADS are still marketed including DADS/Engine, developed in cooperation with BMW. PolyFEM is no longer marketed, however.
Computers and Structures, Inc.
One of the early pioneers in the FEA area was Dr. Edward L. Wilson at the University of California at Berkeley. He was the original developer of the Structural Analysis Program (SAP) which was first released in 1970.
Computers and Structures (CSI) was founded in 1975 by Ashraf Habibullah to market and support SAP which is still widely used today, particularly for the analysis and design of civil structures. CSI products are licensed to thousands of structural engineering firms throughout the United States and in more than 100 other countries. The current package, SAP2000, is intended for use on structures such as bridges, dams, stadiums, industrial structures and buildings. Other software has been developed specifically for multi-story building structures, such as office buildings, apartments and hospitals.
MARC Analysis Research Corporation
Although it never became a major player in the mechanical CAE world, MARC Analysis Research Corporation was one of the industry’s pioneering firms. The company got its start in 1965 when a group of researchers at Brown University in Providence, Rhode Island began development of finite element software which eventually became a commercial package also called MARC.
The company was founded in 1971 and the first version of the MARC software was introduced in 1972. Over the years, MARC became one of the leading vendors of non-linear analysis software. A brief word about what is meant by non-linear analysis may be in order.Much of the world we live in is not necessarily linear in nature. Materials such as rubber respond far differently to loads and constraints than do most metal objects. Examples are car door seals, shock mounts and gaskets.
Metal products also react differently while being formed than they do in operation. A good example is a part fabricated by hot forging. The hot metal is in an elastic state while it is being shaped by rigid dies. As the material cools, the part’s shape changes. The process is further complicated by the fact that even fairly massive dies will deform during the forming process. MARC’s non-linear FEA software was used to make this process more predictable and to reduce many of the physical prototypes previously required.
One of MARC’s early employees was David Hibbitt who completed his Ph.D. thesis at Brown University in 1972. The thesis involved computational mechanics based on the finite element method. The software he developed at Brown formed the basis for the initial version of MARC. MARC was made available to users on a time-sharing basis, particularly via Control Data Corporation Cybernet service. CDC provided access to MARC throughout the 1970s and into the 1980s. Hibbitt remained with MARC until 1977 at which time he left to begin the development of the ABAQUS FEA software as discussed earlier.
The MARC software was a general-purpose FEA program intended for advanced engineering analysis. It supported over 130 different element types, facilitating the modeling of everything from thin shells to cables. MARC incorporated an adaptive meshing methodology that increased the number of elements being used until a preestablished error criteria was satisfied. The company paid particular attention to modeling gaps between parts and taking into consideration how stresses and temperatures propagated between parts that were constantly or intermittently in contact with each other. The software specifically handled situations where a deformable object (perhaps a rubber mounting) contacted a rigid surface.
Although MARC could accept Finite Element Meshes generated by third party software packages, the company offered its own modeling program, Mentat II. This package enabled a user to either import geometry from CAD systems or the geometry could be created directly in Mentat II. In 1996 the latter approach was improved by incorporating Spatial Technology’s ACIS geometric kernel into Mentat II.
In the mid-1990s MARC sought to broaden its customer base by offering application specific solutions. One of these was MARC/AutoForge. This program applied FEA to both hot and cold metal forming such as what was found when using forging, extruding, rolling and multistage manufacturing processes. The basic technical problem in applying FEA to these procedures was that as the metal was deformed, the finite elements used to model the part were also deformed. Very quickly, the model ceased to provide accurate results. MARC/AutoForge addressed this problem by continually remeshing the model as it analyzed each step of the forming process.
Between the late 1970s and 1992, MARC was a well respected but rather minor player in the FEA market. In 1992, the company hired Lou Crain as president and CEO. Crain had been with PDA Engineering from 1975 to 1989 including serving as head of that company’s PATRAN division. By 1996 Crain had built up MARC’s revenue to about $20 million annually, a level it sustained for the next several years.
The financial backers of the company decide that MARC was not going to become a major player in this market and Crain left in late 1998. In May 1999 the company was acquired by MacNeal-Schwendler Corporation (now MSC.Software as described below) for $36 million.
Mechanical Dynamics Incorporated (MDI)
Mechanical Dynamics Incorporated was started as a consulting firm in Ann Arbor, Michigan by a group of University of Michigan engineers in 1977. Among the founders were Michael Korybalski and John Angell who both stayed with MDI for several decades, Korybalski as president and CEO and Angell as chief technologist. The third founder was Milton Chace who was a professor of mechanical engineering at the university. The three had developed a two-dimensional mechanisms analysis package called Dynamic Response of Articulated Machinery (DRAM) prior to starting MDI. The company’s early offices were above an ice cream shop near the U of M campus.
MDI’s early work soon led it to concentrate on analyzing mechanical mechanisms. Engineers are faced with two major problems when designing objects that have complex moving parts – will the mechanism move in the manner expected and what loads are exerted on the these parts as the object moves through its range of motion. As an example, consider a large front-end loader user in mining operations. If the unit is standing still, the designer can estimate the forces on each part of the mechanism when the bucket is in a particular orientation. But what if the loader is moving while raising the bucket and one wheel drops into a large hole?
The firm’s product suite was called Automatic Dynamic Analysis of Mechanical Systems (ADAMS). There were a number of different modules used for building models, solving mechanism equations, verifying the basic motion of a proposed design, simulating complex operations and viewing the results. A major portion of the company’s business came from manufacturers of automobiles and trucks. MDI developed ADAMS modules specifically for this industry including ADAMS/Vehicle which was used to help design suspension systems as well as study the handling qualities of proposed vehicles.
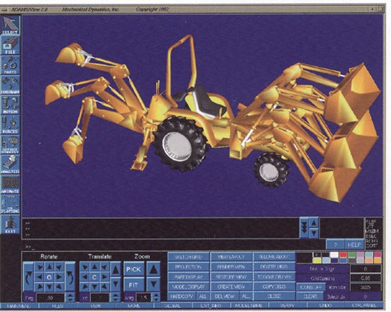
ADAMS ran on a variety of 32-bit computers, including those sold by Digital and Prime as well as UNIX workstations and PCs. In the mid-1990s the ADAMS Full Simulation Package which included both ADAMS/View and ADAMS/Solver sold for $24,000 on UNIX platforms and $10,000 on PCs.
MDI went public in mid-1996 at which time the company had annual revenues of about $25 million which increased to $57 by 2001. In March 2002, MDI was acquired by MSC.Software in a cash deal worth approximately $120 million.
Moldflow
Most plastic parts are produced using a process called injection molding. Once a part is designed, a mold is machined that corresponds to the shape of the part. This mold is placed in a molding machine and hot plastic is injected into the mold. After the plastic cools it can be removed and the process repeated. The objective is to rapidly produce parts that when cooled, do not shrink or warp and faithfully represent the initial design. Prior to the introduction of mold analysis software, this was a trail and error process that often required several sets of molds and cooling lines in order to produce acceptable parts.
Moldflow Pty. Ltd. was founded in Australia in 1978 by Colin Austin and shortly thereafter introduced its first software package for analyzing plastic injection molding processes using a form of finite element analysis. The intent of this software was to determine if plastic at a specified temperature would flow into all parts of the mold and if that plastic would uniformly cool.
Throughout the 1980s and early 1990s, the company’s business model was primarily to negotiate joint marketing agreements with mainstream CAD software vendors. Nearly every such company offered interfaces to the Moldflow software and many resold the package. In the mid-1980s the company opened several design centers around the world which were not particularly successful from a financial point of view. In 1987 Austin hired Hugh Henderson to take over day-to-day management of the company. One of his first steps was to close the design centers. Some of the individuals running these centers set up their own independent mold design businesses.
By mid-1989, Moldflow’s software was available on 18 different platforms ranging from PCs to Cray supercomputers. The company’s products included:
- Moldflow for mold filling analysis
- Moldtemp for mold cooling analysis
- MetlFlow for predicting the filling of die castings.
The software was priced based upon the class of processor it was being run on. At the time, these costs ranged from $6,000 to $30,000 per year for each package. The company was also working on a package to do shrinkage and warpage analysis.[6]
In June1996, Marc Delude, who had been a marketing vice president at PTC, became president and CEO of Moldflow and the company’s headquarters were relocated from Australia to the United States. Current corporate headquarters are in Framingham, Massachusetts.
By 1997, there were over 4,500 users of Moldflow Dynamic Series software in over 50 countries.[7] At this point, the company had about 100 employees and revenues of $16 million annually. In addition to the Dynamic Series’ comprehensive set of analysis capabilities (this software started at $39,000 for a workable suite of modules), the company introduced a lower cost package called Part Advisor in 1997. It was priced at $9,000 for single license.
Part Advisor software was tightly integrated with a number of different CAD packages including Pro/ENGINEER and SolidWorks. It used a simplified approach to define part data for analysis and included a materials library that made selecting plastic materials quite easy. Analysis results such as the time for filling the mold were represented in color coded visual images.
One particularly relevant output was a “Confidence of Fill” diagram that showed those areas of the part where there was a high, medium or low confidence that the part would fill correctly. Based on this output a designer might change the shape of the part, modify the locations where the material was injected, change the temperature of the material or even change the type of material. The software significantly improved the productivity of the injection molding process as well as reduced the time it took to initially produce acceptable parts. Numerous other mold analysis packages have been introduced by the company in subsequent years.
Moldflow went public in 2000 and subsequently acquired C-MOLD, another significant vendor of injection molding analysis software. As this is being written in mid2007, the company’s stock price is about $23.00 per share. This is far better than the low of $4.00 in October 2002 but still below the $30 it hit in early 2001. The company’s revenues are about $70 million annually – more than four times what they were a decade earlier. It currently has slightly over 300 employees.
Roland Thomas, who had joined the company in 1982 in Australia and served as vice president of R&D from 1997 to 2002 became president and CEO in June 2002, replacing Delude.
MSC.Software (McNeal-Schwendler Corporation, PDA Engineering, Mechanical Dynamics, Knowledge Revolution, MARC Analysis Research Corporation)
Today’s MSC.Software is an assemblage of a number of companies that for many years were competitors. Most of these are described separately in this chapter while this section focuses primarily on MSC itself. Much of the early history of MSC is derived from a fascinating book written in 1988 by one of the company’s founders, Dr. Richard MacNeal. Called The MacNeal Schwendler Company – The First Twenty Years, it was a limited edition book published by the company that talks frankly about the struggles of getting FEA accepted as an engineering technology.[8]
MSC was founded in 1963 by MacNeal and Robert Schwendler. Prior to starting MSC, MacNeal received a Ph.D in electrical engineering from California Institute of Technology in 1949 and joined the school’s faculty working in its Analysis Laboratory. At the time, engineering analysis was mostly done on analog computers. A number of the laboratory’s staff members including MacNeal formed Computer Engineering Associates (CEA) in 1952 to commercialize the laboratory’s work building analog computers. MacNeal continued on the CalTech faculty until 1955 at which time he went to work for Lockheed. He returned to CEA a year later, eventually becoming manager of engineering analysis.
MacNeal met Bob Schwendler in 1960 when he visited General Dynamics’ Convair plant in Fort Worth, Texas. Schwendler was the engineer in charge of an analog computer used to simulate aircraft designs. MacNeal offered Schwendler a job at CAE which he accepted.
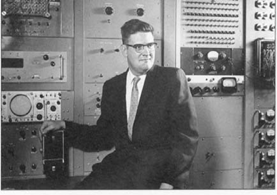
MSC was formed by MacNeal and Schwendler in early 1963 with Arlyn Winemiller, who had joined CAE from Martin in Denver as the third founder. The company was started with $18,000 provided by the three founders. The only other employee was Grace Hunter who had been MacNeal’s secretary at CAE. MSC’s initial business was intended to be engineering consulting and analysis although they were not sure if the latter would be done on analog or digital computers. The company’s first project was the analysis of an arch dam for which they wrote their first FORTRAN computer program which was named SADSAM (Structural Analysis by Digital Simulation of Analog Methods). During the company’s first year it had revenues of about $90,000 and made a profit of $866. SADSAM was used by MSC until 1976 and its use was continued by Hughes Helicopter at least until 1988.
The most significant project in the history of MSC was, of course, its work on the development of NASTRAN (NASA Structural Analysis). By 1964 several aerospace firms had developed proprietary FEA software but there was no generally available software that engineers at other companies or universities could use. About this time NASA began putting together the specifications for a generalized FEA program and a Request For Proposal was distributed in July 1965. MSC decided to team with Computer Sciences Corporation in bidding for this work after being unable to reach agreement with IBM or Lockheed. Martin Aircraft, located in Baltimore, Maryland, subsequently became the third member of the team. In December 1965 the MSC team of which CSC was the prime contractor, was awarded one of two contracts to prepare a Technical Evaluation Report. The other contract was awarded to a team led by Douglas Aircraft. MSC’s report was submitted in the spring of 1966 along with a proposal to implement the software at a cost of somewhat over $1 million.
The MSC team was awarded a contract for the development of NASTRAN[9] in July 1966. MSC was responsible for defining the analytical aspects of the software while CSC personnel did the actual programming. Much of the mathematical work was done by Professor Caleb W. (Mac) McCormick of Caltech who took a leave of absence to work on the project and subsequently joined MSC as a full time employee. Development of NASTRAN was delayed by the need to resolve a number of technical issues fundamental to FEA processes and the lack of available NASA computers. Most of the programming work was done on IBM 7094s and CDC 6600s although towards the end, IBM 360 computers played a major role. The software was delivered to the Goddard Space Flight Center in 1969. Although small by today’s standards, the program was able to handle problems with over 10,000 degrees of freedom.
Between 1965 and 1970 MSC received a total of $635,000 from CSC for its work on the development of NASTRAN. This version of the software eventually became known as COSMIC NASTRAN. COSMIC was a federally funded program run by the University of Georgia which was used to distribute government developed software for a small reproduction fee. Initially, the fee for COSMIC NASTRAN was $1,750. NASTRAN was a large program consisting of over 150,000 FORTRAN statements. During this period, MSC continued to develop and market analog computer components although by 1972 this activity was generating very little revenue.
Beginning around 1969, MSC began developing a consulting practice involved in assisting companies interesting in installing and utilizing NASTRAN including Vought, Aerojet and Bell Helicopter as well as a number of government laboratories. MSC was also awarded several NASTRAN maintenance contracts by NASA starting in June 1971 with Control Data Corporation acting as a programming subcontractor. This arrangement continued until early 1974 when NASA and MSC parted ways over the NASA’s perception that MSC was taking unfair advantage of this contract in regard to its other consulting business.
The MSC and NASA versions of NASTRAN began diverging as early as 1971 leading to the company’s proprietary implementation being called MSC/NASTRAN. The company began to offer MSC/NASTRAN to other companies for a support fee of $500 per month. The first customer under this arrangement was McDonnell Douglas in Saint Louis, Missouri. The company also began providing its software to service bureaus on a royalty basis. CDC Cybernet soon was producing 60 percent of MSC’s lease and royalty revenue. For the next several decades, charging a monthly or annual fee for its software rather than selling fully paid licenses became a basic business characteristic of MSC. The company opened a European office in Munich, Germany run by Leonard Peterson and an office in Japan run by H. Watanabe. Mac McCormick was instrumental in both of these international efforts, even going to the point of learning Japanese in order to better work with Japanese customers.
MSC continued to rapidly expand its version of NASTRAN with new element types and new analytical processes. By early 1976, less than 30 percent of MSC/NASTRAN contained the same code as COSMIC NASTRAN. New capabilities included a preprocessor developed in Germany by Peterson called MSGMESH. By this point MSC/NASTRAN was being used to solve problems with as many as 30,000 degrees of freedom. By 1978 MSC had 85 contracts for the use of MSC/NASTRAN and royalty revenue that year was nearly $1.4 million, the majority of which came from contracts with data centers such as CDC. MSC was now charging its industrial customers $1,000 per month for MSC/NASTRAN while NASA has raised its fee for COSMIC NASTRAN to $4,000 per year.
For the most part, MSC was conservatively managed during the 1970s. From 1970 to 1976, the company had about 20 employees. It started to grow rapidly from that point forward as revenues, mostly from MSC/NASTRAN, increased 40 percent annually.
Dr. Joseph Gloudeman joined the company in 1978 from Rockwell. MacNeal was enthusiastic about recruiting him since Glouderman brought a degree of management experience that the company’s then current executives lacked. He was also seen as a possible successor to MacNeal who was 55 at the time. Initially hired to head marketing and advanced product development, Glouderman became president and COO shortly before the company went public in May 1983.
In 1979, the company opened an a regional office in New England with Dr. Harry Schafer in charge. Actually, a new company was established called Shaffer Analysis, Inc with MSC owning 80 percent. Shaffer had been a professor at the University of Maryland and his principal role was to continue training people to use FEA with emphasis on MSC/NASTRAN. Shaffer also ran a series of conferences in the early 1980s on FEA technology called the Chautauqua on Finite Element Modeling. Schaffer’s relationship with MSC lasted for several years at which time he purchased MSC’s interest in his company for basically what MSC had originally invested.
Until 1978, MSC/NASTRAN was supported on mainframe computers from CDC, Univac and IBM. These were expensive machines and MSC was unable to afford a machine of its own. This situation changed with the introduction of 32-bit computers such as the Digital VAX 11/780. In mid-1978 MSC negotiated an agreement with Digital to port its software to this new machine and installed an 11/780 that fall. Within a few months, the company had MSC/NASTRAN up and running and by January 1983, there were 64 customers using this machine.
A major change took place when Bob Schwendler passed away unexpectedly on January 2, 1979. Mac McCormick was made executive vice president in his place and Joe Glouderman became vice president of marketing.
In addition to the VAX 11/780. MSC began supporting a wide range of other computers ranging from the Apollo engineering workstation to the Cray supercomputer. Software development during the early 1980s focused on adding nonlinear capabilities as well as work on pre- and postprocessors. A new package in this latter area, MSC/GRASP, was released in 1982. Many MSC customers, however, used PATRAN software from PDA Engineering for this function.
For over a decade, the relationship between NASA and MSC had been basically problem free. This came to an abrupt halt with a letter dated August 26, 1980 in which NASA claimed that MSC had inappropriately been using software code developed as part of NASTRAN maintenance work MSC performed for NASA in the early to mid-1970s.
This letter was a result of an audit NASA had initiated more than a year earlier.
According to MacNeal, the audit was most likely the result of a complaint lodged by Tony Cappelli, the president of Universal Analytics. This company resold a version of COSMIC NASTRAN it called UAI/NASTRAN.
The dispute with NASA dragged on for over two years until it was settled with MSC paying NASA $125,000 for all rights to use the software it had previously developed under its contracts with NASA. This was far less than the several million dollars the government originally wanted. Resolution of the problem was critical in that MSC was preparing to go public. The public offering took place on May 5, 1983 at an initial price of $29 per share. The stock closed that day at $36.75. In the process, the company raised approximately $10 million while stockholders sold over $25 million of stock. MSC’s stock was listed on the American Stock Exchange. Joe Glouderman became CEO in March 1985, at which point Dick MacNeal retired. This lasted until 1991 when the company’s earnings came up short. Glouderman was pushed out as CEO and MacNeal rejoined the company as president and CEO.
The company continued to grow at a fairly consistent pace with annual revenues reaching $65 million and earnings of $12 million for the year ending January 31, 1993. Software development included the introduction electromagnetic analysis (MSC/EMAS) and dynamic analysis (MSC/DYTRAN) as well as the support of a growing number of computer systems including Hewlett-Packard and Sun Microsystems workstations. The company continued to license its software on an annual basis as well as beginning to sell fully paid-up licenses with the cost determined by the power of the computer being used and the maximum size models that could be analyzed.
A new pre- and postprocessor, MSC/XL was introduced as well as a version that incorporated software from Aries Technology (see Chapter 21). The latter was called MSC/XLplus. The relationship with Aries eventually led to MSC acquiring the company for $20 million in September, 1993. With this acquisition, Larry McArthur became president and COO while Dick Miller became MSC’s vice president of corporate marketing and general manager of the Aries Division. The other key member of the management team was Dr. Dennis Nagy who was senior vice president, operations. One byproduct of the Aries acquisition was that the people at MSC’s headquarters who were working on MSC/XL were reassigned to the Aries division. On the flip side, Aries sales organization was absorbed into MSC’s sales operation.
The Aries acquisition was followed less than a year later by the acquisition of PDA Engineering (see below) for $56 million. At the time, MSC was an $80 million company while PDA was doing $42 million annually. The acquisition was driven by two observations. First, MSC’s management felt that the mechanical design market was on the verge of significant consolidation – a position that proved to be particularly perceptive although it might have taken longer than they expected. The other observation was that the two companies were spending disproportionate resources developing software to compete with each other. The plan was that Aries would provide software targeted at the design engineer while PDA would target the professional analyst. Lou Delmonico, PDA’s CEO at the time of the acquisition left soon after the deal was completed but Tom Curry, PDA’s president and COO stayed with the merged company.
The acquired products were renamed MSC/ARIES and MSC/PATRAN, respectively. McArthur left MSC in late September 1994 and Miller left several months later. The company announced that it had initiated a search for a new president and CEO. In November 1994, MSC demonstrated a Windows version of MSC/NASTRAN price at $5,000 per copy. On the financial side, the company was struggling to increase revenues of the combined PDA and MSC business. It took until 1996 before it was heading in the right direction.
Like most other FEA software firms, MSC worked hard to increase the performance of its analysis software. MSC/NASTRAN Version 68.1 released in mid1995 was significantly faster than prior releases, enabling users to tackle larger models in a reasonable amount of time. The company also began to work more closely with CAD software firms, probably influenced by personnel who joined the company as a result of the Aries and PDA acquisitions. One example was that in late 1995, MSC signed a joint development and marketing agreement with EDS Unigraphics and an agreement with Matra Datavision under which the latter company distributed QUICKSOLVER, a subset of MSC/NASTRAN.
MSC promoted Curry to president and CEO in March 1996. A few months later, the company decided to focus on structural analysis issues and sold its electromagnetic analysis business to Ansoft for $5.6 million. MSC began to concentrate on specific market segments. The company set up an aerospace unit under Kenneth Blakeley and an automotive unit under Thomas Tecco.
One significant development in August 1997 was the release of a Windows version of MSC/PATRAN. This was followed in November by the launch of MSC/InCheck which provided stress, vibration, and buckling simulation inside SolidWorks 97Plus. A few months later a new version added shape optimization and steady-state heat transfer simulation to the package. In December 1998, Curry was replaced as president and CEO by Frank Perna, Jr. who also became chairman, replacing George Riordan who had been serving as chairman. Perna had previously been CEO of EOS Corporation, a high technology electronics manufacturer. About the same time, MSC announced plans acquire Knowledge Revolution, the vendor of the Working Model suite of motion simulation software for $19 million in cash.
In March 1999 the company announced plans to change its name to MSC.Software to reflect its growing interest in providing software and services via the Internet. In May 1999 the company acquired MARC Research and Analysis Corporation for $36 million. This was followed in July with the acquisition of Universal Analytics, the vendor of UAI/NASTRAN and in November by the acquisition of Computerized Structural Analysis and Research Corporation (CSAR) the vendor of CSA/NASTRAN.
At this point, MSC controlled over 95 percent of the NASTRAN software market which caught the attention of the Federal Trade commission. After several years of hearings and negotiations, MSC agreed to a consent decree that provided in part:
“The principal relief under the proposed Order is to require the Respondent to divest, within 150 days after entry of the Order and to up to two acquirers to be approved by the Commission, perpetual, worldwide, royalty-free, and non-exclusive licenses to the key intellectual property needed by a new competitor to compete in the sale and licensing of advanced Nastran software.”[10]
Soon after the consent decree was finalized, MSC negotiated a license agreement with EDS PLM Solutions (The name of UGS at the time) for that company to develop and market its own version of MSC/NASTRAN.
In addition to acquiring most of the independent NASTRAN vendors, Perna had the company expand its Internet offerings. In February 2000, MSC announced a new Web environment that encompassed its entire product range. This new offering was referred to as MSC.visualNastran and it tied together all the disparate systems the company had developed or acquired as modules under a single framework.
The company’s engineering-e.com Web portal offered Web-based software (e.visualNastran), on-demand licensing for stand alone software, stand alone software (Visionary Design Systems’ IronCAD), text books and training. e.visualNastran used the same interface as regular MSC.visualNastran. Users could lease it by the month and results could be stored at the MSC computer site. It was touted as the first analysis program available via an Application Service Provider (ASP). A new MSC.Linux division was created to support several large customers that were already adopting Linux as a sanctioned operating system for Intel-based computers. Many of the MSC programs were subsequently ported to Linux.
In May 2001 MSC.Software announced that it was buying privately held Advanced Enterprise Solutions, Inc. (AES), a major North American CATIA dealer that also sold products from Autodesk and others software vendors as well as computer hardware. MSC agreed to pay $130 million in a combination of cash, shares and notes. One result of the merger was that Dassault, which owned 19 percent of AES ended up owning nine percent of MSC.Software. With this acquisition, the company’s annual revenue went over $200 million.
The next major acquisition the company made came in March 2002 when MSC announced that it was acquiring Mechanical Dynamics Incorporated for $120 million in cash as mentioned earlier in this chapter.
One problem with the AES acquisition was that its business, which mostly consisted of reselling hardware and software, was a low margin business and one that could fluctuate substantially quarter to quarter. In May 2002 MSC laid off about eight percent of its staff or 140 people. This brought the headcount down to about 1,500. Revenue continued to fluctuate widely quarter to quarter and in mid-2003 the company announced that it would no longer resell computer hardware, what had been a $20 million per quarter business. This resulted in a $25 million restructuring charge. While the MDI acquisition looked very good, the AES deal was turning into a financial quagmire.
In February 2005 William Weyand replaced Frank Perna as Chairman and CEO of MSC.Software. Then in August, Glenn Wienkoop was hired as president and COO. Both had previously worked for SDRC prior to its acquisition by UGS. Annual revenue in 2006 was about $300 million.
Dick MacNeal was not done with FEA technology just yet. Together with Dr. Harry Schaeffer who had founded Schaeffer Automated Simulation, LLC in May 2000, McNeal founded The MacNeal Group (tMG). Joining them were several experienced FEA development and marketing individuals (Mark Kenyon, Ted Rose and Mike Krauski) each of whom had each spent a number of years at MSC and had earlier joined Schaeffer Automated Simulation. tMG’s market focus has been to offer low-cost analysis software built around the original NASA NASTRAN code.
PDA Engineering (Prototype Development Associates)
PDA Engineering was established in 1972 as Prototype Development Associates to work on defense and aerospace projects involving materials technology and structural analysis. To support this work, the company began developing software packages, especially software to build models for FEA.
In 1977 the company began to turn this work into a commercial product for mechanical design and analysis. Designed to function as a pre- and post-processor for FEA programs offered by other companies as well as proprietary packages, the software, PATRAN, was introduced in 1979. In 1980, the company changed its name to PDA Engineering. Gradually, the company’s focus shifted from engineering services to software licensing. PDA Engineering went public in 1985.
By 1986, the company’s revenues (for the fiscal year that ended June 30th) were $17.4 million of which software represented 56 percent of the total. The company reported 535 commercial PATRAN licenses in use as well as 92 university agreements. The company’s president was Dr. John McDonald, one of the company’s founders, while the PATRAN activity was run by Louis Crain. Hayden Hamiliton, who previously was with SDRC, was executive director of software development while Jim Newcomb was director of marketing and Rick Caselli was director of sales. Newcomb had previously been with Auto-trol Technology and Dataquest, an industry market research firm, while Caselli had earlier been with Applicon.
Crain was the key person at PDA during PATRAN’s formative years. He had a degree in aeronautics and astronautics from MIT and had worked on NASA’s Apollo and Skylab projects while employed by McDonnell Douglas. He joined PDA in 1975 and remained with the company until 1989. At various times he was either vice president or president of the PATRAN division.
In 1988, PDA Engineering began development of a new version of PATRAN called PATRAN 3. While earlier versions of the software had been implemented on the basis that the user would interactively create the FEA model either using data imported from a CAD system or geometry created directly by the user, PATRAN 3 was predicated on the assumption that models would be created directly from CAD data.
The company became more aggressive in developing partnership agreements with CAD vendors including EDS/Unigraphics, Dassault Systèmes, PTC and Matra Datavision. PDA referred to this approach as “The Single Geometric Model.” A key aspect of the new software was that loads and boundary conditions could be applied to the geometric model and if the geometry of the model changed, the loads and boundary conditions would still be associated with the model.
PATRAN 3 was publicly announced on October 1, 1991 but was not ready for customer delivery until mid-1992. This was a large project that was a ground-up restructuring of the software that implemented a MOTIF-compliant user interface, initially on Sun workstations. PDA provided interfaces to both MSC/NASTRAN and ANSYS as well as FEA software it had developed or licensed from other companies. By 1994, PDA had invested over $35 million developing this software.
The company also offered two other products. One was M/VISION, introduced in 1990, that enabled users to visually review material information contained in either industry databases or information that had been developed internally. The other product was DESIGN/TEAM (Trimmed Element Analysis Method) that used an analysis technique often referred to as the Boundary Element Method. The latter technique differed from the traditional FEA method in that it worked directly with the geometry that described the part. DESIGN/TEAM was conceptually similar to software marketed by Rasna Corporation (which was subsequently acquired by PTC as discussed in Chapter 16). DESIGN/TEAM was renamed P3/TEAM and incorporated into the PATRAN 3 product in early 1994.
PDA’s business seemed to be on a roll until mid-1993. In August 1993, the company announced that its earnings for the 4th fiscal quarter of 1993 which ended that June 30th had dropped to $0.10 per share from $0.17 the prior year. The price of the company’s stock dropped from $11 per share earlier in 1993 to $3.75 after the announcement. One result of PDA’s changing fortunes was the only criminal conviction I am aware of involving investments in a CAD industry company.
Richard J. Smith was vice president of North American sales for PDA at the time.
He had previously been employed at Auto-trol Technology in sales and marketing. In mid 1993 he became aware of the company’s revenue shortfall for the quarter and the adverse impact that would have on 4th quarter earnings. He proceeded to sell over 50,000 shares of PDA stock and sold short another 35,000 shares. In addition, he provided this nonpublic information to a close friend, Angela Bravo de Rueda and his father, David Smith.
The Securities and Exchange Commission filed a complaint in September 1995 based on a voice mail message Smith had left for several other PDA employees. This voice mail message was heard by another employee, Linda Grove, who for some reason was listening to other employees voice mail. She forwarded the message to her own voice mail box and recoded it. She then disclosed this message to PDA management which led to an SEC investigation. The SEC claimed that Smith had made over $120,000 in illegal profits from his actions.
In March 1995 the SEC enjoined Smith from further violation of federal security laws. This was followed by a criminal conviction in 1996 at which time he was sentenced to serve 15 months in prison and pay over $95,000 in restitution and fines. As far as I could determine neither his father nor friend were prosecuted.
The downturn in PDA’s sales led to losses in fiscal 1994 and eventually to the company’s acquisition by MacNeal Schwendler Corporation in August 1994 for $6.85 per share or a total of $56 million. At the time, PDA’s sales were running at about $42 million per year.
Structural Research & Analysis Corporation
Structural Research & Analysis Corporation (SRAC) was founded in Los Angeles in 1982 by Dr. Victor Weingarten a professor at the University of Southern California and the head of its civil engineering department. The company’s early software was mainframe oriented but by 1985, SRAC’s focus had switched to personal computers and engineering workstations. As I wrote in Engineering Automation Report in November 1995, it took a great deal of foresight to realize in the mid-1980s the impact desktop computers would have on engineering design.[11]
Throughout the 1980s, SRAC launched several versions of COSMOS, its flagship FEA package. The company grew slowly as it focused on its software development efforts. At one time the company offered a version of its COSMOS software on the Apple Macintosh but soon decided to concentrate on MS/DOS PCs and UNIX workstations.
In the mid-1990s SRAC began developing closer working relations with the companies producing a new class of mid-range CAD software packages including Bentley Systems, SolidWorks, Intergraph and Autodesk. The intent was to provide design engineers with sufficient FEA technology that they could perform first level analyses on the parts and assemblies they were designing. The first such collaboration was with Bentley Systems. This resulted in a package called COSMOS/M DESIGNER II in 1995 followed by COSMOS/Works in 1996 with SolidWorks.
In addition to creating the ability to work directly with CAD geometry, SRAC programmers spent a substantial amount of effort creating fast algorithms for solving FEA problems. The company’s flagship code in this area was simply called FFE for Fast Finite Element.
By 1998, COSMOS users were processing surprisingly complex FEA models on Pentium II PCs. One example was Nichols Aircraft which manufactured lubricating oil pumps for the jet engine industry. With the help of SRAC’s consulting staff, Nichols engineers created a complete FEA model of a pump casting with approximately 1.3 million degrees of freedom in three to four days. First order solutions on a PC took less than two hours to run. Just a few years earlier, most analysts would not have attempted a problem this size on anything less than a mainframe or expensive high-end server.[12]
At the same time, SRAC was developing new software using UGS’s Parasolid solids modeling technology that would enable users to directly build FEA models from packages such as SolidWorks, Solid Edge and MicroStation Modeler, all of which also used Parasolid. This technology was called DesignSTAR and was intended to facilitated linear static and dynamic analysis as well as thermal analysis. The first actual product to use this technology was called COSMOS/Edge 3.0 which worked with Solid Edge. It was priced starting at $5,000.
In 1999, SRAC introduced COSMOS/Works 5.0 which could be embedded in SolidWorks 99. This enabled users to design parts and assemblies and to analyze them in a continuous operation without the need to translate data from one package to another. The software included a new meshing capability called AccuStress that automatically changed the density of elements in areas where higher stresses could be expected. Previously, this was a time-consuming manual process and not one design engineers were particularly good at. Cosmos/Works could also be used to optimize the shape of parts.
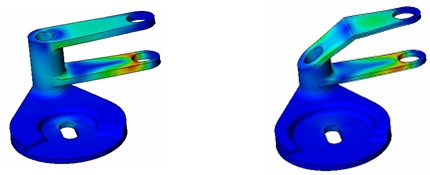
The relation between SRAC and SolidWorks became increasingly close in subsequent years and in March 2001, Dassault Systems acquired SRAC for $22 million in stock and eventually made it part of the SolidWorks operation. Initially Barbara Guerra, Victor Weingarten’s daughter and vice-president of sales and business development at SRAC and, became CEO of the new subsidiary. Dr. Vasu Chavakula, vice-president of engineering and Lih Wu, the company’s CFO and director of international sales remained in similar positions under Dassault ownership. President and CEO Dr. Victor I. Weingarten, SRAC’s founder, served for a period of time in a consulting capacity.[13]
In December 2001, SRAC introduced a new package, COSMOSMotion, that integrated MDI’s motion analysis software with SRAC’s structural analysis software. The resultant package worked closely with SolidWorks so that users had only one interface to work with.
Tektronix
Several companies, particularly McDonnell Douglas Automation (McAuto), Boeing Computer Services and Structural Dynamics Research Corporation (SDRC) offered either time-sharing services or software packages for handling the creation of finite element models, formatting the data for analysis and displaying results. The McAuto software targeted civil engineering users while the other were more focused on mechanical engineers.
The biggest problem with time-sharing solutions was that the terminal had to be continually connected to the main computer system over links that were 2,400 bps at best. The terminals available at the time had very little local intelligence. Since the typical model involved a substantial amount of data, simply tasks such as rotating the model to a new orientation were quite time consuming since the entire image had to be retransmitted by the host computer. In addition, time-sharing was fairly expensive if an outside commercial service was being used.
In 1976 I was the manager of market development for Tektronix’s Information Display Systems division. The company had recently introduced the 4081 graphics system which could function as either a stand-alone computer or as a terminal to a larger computer. Some people have referred to it as the world’s first graphics workstation. The 4081 consisted of a 19-inch storage tube display and an Interdata 16-bit minicomputer.
We decided to create a 4081 program that would handle the creation of FEA models. This project was assigned to a very good software developer, Jeff Gingerich, who, over time, was assisted by Marv Abe, Gary Romans, and others. Although it probably had a different name at the start, this system, which included both the 4081 hardware and the software, became known as the FEM181.
The intent was to create a 4081 software package that would enable a user to interactively build a FEA model completely off line and would require connection to the computer being used for analysis simply to upload the completed model and download results. The FEM181 system did not include post-processing software as such but the general graphics capabilities of the 4081 could be used for this function if the user organization wanted to write that software. Models could be created in three different modes – existing model data could be downloaded from a host computer and edited, element data could be entered by digitizing drawings or elements could be created interactively.
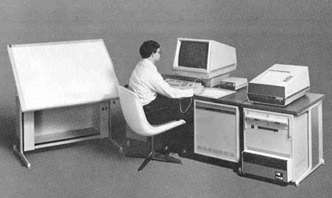
Downloading existing data was important since many potential users already had models that had been created using traditional methods and wanted to use the FEM181 to edit and update that data. I am not sure how it came about, but Jeff and I came up with the idea of being able to graphically shrink each element when it was being displayed without actually changing the model data. When a model is displayed, elements that are adjacent share common boundaries. If an individual element was missing, the user might not realize that fact because all the edges appeared to be displayed. By shrinking every element towards its center, gaps would appear between elements. A missing element would jump right out at the user.
When the system was demonstrated to Chrysler, a finite element model of a automobile hood was downloaded to the FEM181 system. The applications engineer doing the demonstration did a shrink operation on the model and the manager in charge of the Chrysler analysis department took one look at it and said “So that’s why we have been getting poor results with this model.” Right in the middle of the model was a missing element. It was not obvious in plots of the input data but it caused the FEA program to produce erroneous results. Within a few years, virtually all FEM packages incorporated this capability.
The FEM181 was launched in the summer of 1977. Over the next several years probably 20 systems were sold and installed. Some of these were used well into the 1980s. Tektronix withdrew from the systems business in late 1979 and other companies such as PDA Engineering (now part of MSC.Software) began offering comparable software.