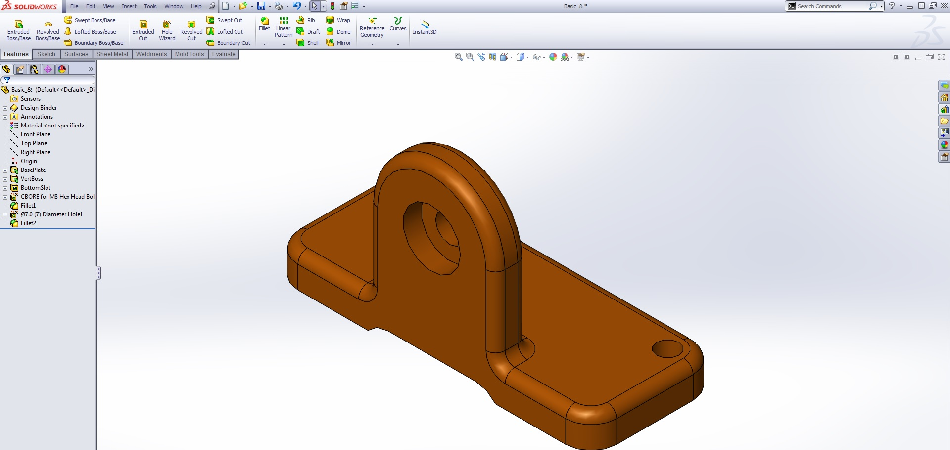
As much as any company in the CAD industry, SolidWorks was inspired by the vision of a single individual, Jon Hirschtick. He received both a BS and an MS degree in mechanical engineering from MIT in 1983 and subsequently worked at the MIT CAD Laboratory under Dr. David Gossard. Hirschtick had a strong entrepreneurial streak in him from an early age including a period as a self-employed magician during high school. While working at the CAD Laboratory, he enrolled in an entrepreneurship class in 1987 where he teamed up with Axel Bichara to write a business plan for a new CAD software company they called Premise. Bichara was a graduate student from Germany who was also working at the CAD Laboratory at the time.[1]
The class business plan for Premise was submitted in mid-May, 1987 and in a little over a month the two founders had $1.5 million in venture funding from Harvard Management Company. It was no surprise that the company set up shop in Cambridge.
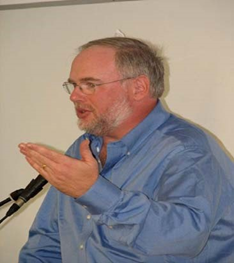
Premise’s initial software product, DesignView, was a two-dimension conceptual design tool that ran on IBM-compatible PCs and interfaced with Microsoft software packages such as Word and Excel. Users could sketch geometry, assign constraints and define dimensional relationships. If a dimension changed, the design would adapt to this new information. Since it could be interfaced to Excel, spreadsheets could be used to define parts by linking specific dimensions to cells in the spreadsheet. Design View sold for $1,895 per copy.[3]
While the software was successful in what it did, the market for DesignView was simply too small for Premise to prosper. Computervision acquired Premise and the DesignView software in the spring of 1991 with the intent of marketing DesignView as a conceptual front end to its own CADDS 5 software. Both Hirshtick and Bichara joined Computervision’s management team. Bichara left after about a year to return to Europe where he enrolled in an MBA program at INSEAD in Fontainebleau, France. For the next several years, Hirschtick stayed with Computervision, initially managing DesignView and subsequently responsible for the product definition of other Computervision software.
Getting started as Winchester Design
Hirschtick left Computervision in August 1993 without a clear idea of what he wanted to do next other than run his own company. By January 1994, the idea of creating a low-cost desktop design system based on solids modeling technology began to jell. Hirschtick put together a team consisting of Bob Zuffante, Scott Harris, Constantine Dokos, Tommy Li and himself that started the development of what eventually became SolidWorks.
The founders decided to forego early external funding and worked out of their homes for much of 1994 without pay. They even purchased their own PCs to use for software development. A key addition to the team was Michael Payne who joined the group in August 1994 to manage the overall software development effort. Payne had been PTC’s employee number three and was vice president of development when he left a few months earlier over a management dispute. Prior to PTC, he had been director of CAD development at Prime Computer. Anyone who knows both Hirschtick and Payne probably cannot envision two more distinctly different personalities, yet they worked effectively together for the next six years. The company was initially known as Winchester Design Systems, the name coming from where their first real office was located.
With Payne on board, the company felt that it was time to acquire external funding. Hirschtick had been working closely on this issue with Bichara, who had returned to Boston and was working at Atlas Venture, a local venture capital firm. In fairly short order two other venture capital firms, North Bridge Venture Partners and Burr, Egan, Deleage & Company, joined Atlas Venture and the three provided about $4.5 million in funding.. This investment kept the company going until late 1995 when the same VC firms along with Kubota and other investors put an additional $9.2 million into the company. As part of this latter investment, Kubota became the company’s distributor for Japan.
Another key recruit was Victor Leventhal who came on board in October 1994. Leventhal had had a long sales and marketing career with IBM where he had run a $1B division in the 1970s and early 1980s, had run a $120 million direct sales operation at Computerland and was the CEO of a CAD reseller, CAD Solutions, when recruited by Hirschtick. Leventhal’s responsibility as chief operating officer was to build a reseller channel that was capable of competing with Autodesk’s dealers.
As discussed in Chapter 16, Parametric Technology Corporation, which was started in 1984, had been successful in part because it did not have to support the legacy minicomputer and mainframe-based software that its competitors did. PTC developed Pro/ENGINEER from the start to be hosted on networked UNIX workstations. Its software was written in a higher level language and the system utilized the latest software architecture techniques. But even PTC was limited in the extent the it could use platformspecific operating system code to implement user interface and file management tasks due to the multiple UNIX platforms it was committed to support.
Hirschtick’s plan was very simple. SolidWorks would only run on Windowsbased PCs and the company planned to utilize standard Windows capabilities for as many system functions as possible. The result was a program that had the same Windows look and feel as Microsoft’s own applications including Word and Excel. This approach significantly reduce the amount of software code that Payne and his development team had to produce. Also, if the software was to run on inexpensive PCs, then the price of the software had to be similar. The company settled on $3,995 for the initial release.
As reported in the October 1995 issue of the Computer Aided Design Report: “What distinguishes this CAD software from others is the way these capabilities are controlled by the user. Once you’re familiar with the basics of Windows programs, it’s much easier to create and change parts and assemblies than is possible with any other solids-based system we’ve seen.”[4]
This strategy also took advantage of changes taking place in the PC world. Both Windows NT and Windows 95 were turning out to be well accepted by the user community, the performance of Intel microprocessors was increasing very rapidly and the price of memory decreasing at an even faster pace. As a result, fast PCs with large internal memories were becoming economically attractive.
Early versions of SolidWorks[5]
SolidWorks, while still known as Winchester Design, began quietly showing a prototype of the SolidWorks software to industry analysts and media in late 1994. I believe I first saw the software at the National Design Engineering Show in Chicago in February 1995. This was followed up in late summer by a visit by Jon Hirschtick to Engineering Automation Report’s office in Englewood, Colorado where he personally demonstrated the latest pre-release version of the software.
Hirschtick did a competent job of building individual part models with the software but when I asked that he create a simple assembly, the software failed to cooperate. I never could determine if there was a software problem or Hirschtick was simply not proficient with the assembly functions in SolidWorks.
Initial development used Spatial Technology’s ACIS geometric kernel but long before the software was released the company switched to EDS Unigraphics’ Parasolid due to performance problems and functional deficiencies with ACIS. EDS also offered SolidWorks better licensing terms than did Spatial.
Shortly before the software was to be released, PTC filed a lawsuit against SolidWorks claiming that the latter company had recruited PTC employees in violation of those employees’ non-compete agreements. This could have stalled SolidWorks dead in its tracks but the two companies managed to settle before too much damage was done. It did set the stage for the fierce competition between the two companies that persists to this day.
The formal unveiling of the software, now known as SolidWorks 95, took place at the 1995 AUTOFACT conference. There was no question from the start that one of SolidWorks’ target markets consisted of companies that were considering the purchase of Pro/ENGINEER software. The other competition, of course, was Autodesk and its AutoCAD software. (See Chapter 8.)
SolidWorks 95 was a feature-based, dimension-driven solids modeler that generated two-dimensional drawings directly from the solid model. As with Pro/ENGINEER, a change to the model changed the relevant drawings and going the other way, a change to the drawing was also associated with the model. While a surprising amount of Pro/ENGINEER-like functionality was incorporated into the first release of SolidWorks, there were some differences. Some of these involved modeling capabilities that probably were of interest to a minority of potential customers while other were more strategic in nature. Foreign drafting standards were not supported initially which slowed down the software’s acceptance internationally.
On the flip side, the initial implementation of SolidWorks 95 incorporated features normally associated with more expensive high-end systems. This included the ability to name specific features rather than just numbering them, the ability to use sketches that were not fully constrained and the re-ordering of features using the same technique one would use to reorganize Windows files within a folder or between folders.[6] Models could incorporate algebraic relationships between dimensions so that a change to one dimension could change one or more other dimensions. Other aspects of this new package that appealed to prospects were:
- A graphical user interface compatible with Windows 95 and Windows NT
- A sketcher that automatically applied constraints
- OLE 2.0 enabled files for exchanging model data with other applications
- A constraint manager based on the DCM software from D-Cubed
- The ability to reposition a feature by simply selecting it and dragging it to a new location
- The ability for users to create their own macro commands using the BASIC programming language.[7]
SolidWorks 95 took off with a bang. Most initial releases of new software products have severe functional shortcomings and far too many bugs that prevent productive work from getting done. Not so with SolidWorks 95. According to Computer Aided Design Report: “We’re pleased to report that SolidWorks is one of the nicest – possibly the best ever – first release of a CAD software product that we’ve seen.” The newsletter went on to extol the software’s modeling capabilities, particularly its “Feature Manager” which enabled users to change the sequence in which a model was regenerated or “rebuilt” in SolidWorks terminology. The nested list of elements used to create the design were displayed on the side of the screen at the same time the model was being viewed.
There were some problems with the early software, particularly in the area of assembly modeling and drawing production. Assembly modeling functionality was somewhat limited and if you were not careful, you could insert one part into another. While drafting was judged to be a good start, there were a number of limitations that required workarounds. The CAD Report, was also disappointed with overall performance on mid-range PCs, particularly in regards to photorealistic rendering using PhotoWorks described below. Documentation, or the lack thereof, was also a concern.[8] Most of these complaints were of the type that one could expect to be corrected with the next several releases of the software and they were for the most part.
Jumping on the bandwagon
Fairly early, SolidWorks made it clear to the rest of the CAD industry that it would not develop a direct sales force to compete with its resellers. This resulted in a highly committed group of dealers. Likewise, the company indicated that it planned to focus on the core SolidWorks software and would not be developing a broad spectrum of applications. This position appealed to independent software developers and soon a number of them were offering applications that worked with SolidWorks. In some cases, SolidWorks bundled these application with its own software and sold them as a package while in other cases, SolidWorks took a hands off approach.
One of the first applications was a photorealistic rendering package, PhotoWorks, developed by LightWorks Design of Sheffield, England. It was sold by SolidWorks for $795 or customers could buy the combination of SolidWorks and LightWorks for $4,390.[9] By mid-1996, SolidWorks had signed partnership agreements with 55 thirdparty software developers, seven of whom had already released SolidWorks compatible packages.
One of the most aggressive of these partners was Los Angeles based Structural Research and Analysis Corporation (SRAC). Founded by Dr. Victor Weingarten, SRAC was a vendor of moderately priced finite element analysis software that was reasonably easy to use and quite fast, at least for small to moderate size problems. SRAC repackaged its COSMOS FEA software to work directly with SolidWorks 96. Called COSMOS/Works, it added a FEM menu item to the top of the SolidWorks display. When selected, this menu item took the user out of SolidWorks and into a version of COSMOS tailored specifically to work with SolidWorks model data.
Users were able to create a FEA model from the SolidWorks model, apply loads and boundary conditions, analyze the part and view the results. Both programs had a similar look and feel that conformed to the Windows standards. The intent of this implementation was that a design engineer would be able to do his/her own stress analysis rather than have to involve a structural analysis department staffed with FEA specialists who used high-end FEA software such as ANSYS or MSC NASTRAN on mainframe computers.
This created heated discussions within the engineering community as analysis professionals felt that providing this capability to engineers who lacked sufficient training was a dangerous precedent while the proponents of this approach felt that it would now be possible to analyze far more parts than before and under a greater variety of conditions. There probably was some truth to both sides of the argument.[10]
As with SolidWorks itself, one of the key technology developments powering the increased use of advanced technical software was the rapid increase in computer performance, especially desktop PCs. By late 1998 many engineers had access to 400MHz Pentium II computers for their own use. These machines were capable of analyzing large FEA models that just a few years earlier would have required a mainframe computer. As an example, one SRAC customer, Nichols Aircraft, built an FEA model of one of its jet engine lubricating oil pumps that had 1.3 million degrees of freedom. It took just two hours to run an analysis on a contemporary PC. Between them, SolidWorks and SRAC were changing the practice of engineering design and analysis.
Although SRAC worked with other CAD vendors including Intergraph and UGS, its relationship with SolidWorks was perhaps the strongest and the most tightly integrated version of its software was COSMOS/Works. COSMOS/Works 99 added design optimization capabilities to this product as shown in Figure 18.2.
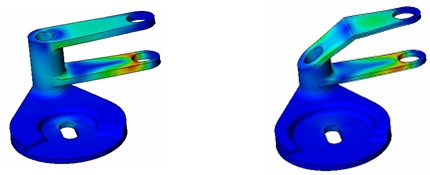
SolidWorks evolves at a fast pace
SolidWorks 96 was released in July 1996 with fixes to many of the early problems mentioned above. In particular, assembly modeling was beefed up significantly. User were now able to design and edit individual parts while in assembly mode. The performance regarding large assemblies was improved by enabling users to load subsets of the models they wished to work with. Drafting was also improved by providing users with more control over the placement of individual views as well as the ability to use three different line weights and multiple text fonts.
Assembly cross sections worked much better than with the initial release of the software. Documentation was substantially improved and rendering performance was more acceptable. There were still some shortcomings that had not been fixed such as the lack of a redo function and the inability to stop long operations such as loading large models by mistake.[11]
Less than a year later, SolidWorks 97 was rolled out with 175 enhancements according to the company. This version of the software incorporated a number of enhancements and corrected problems associated with the first two releases. A new sheetmetal design capability was incorporated into the basic package as was the ability to add raised text to flat surfaces of parts. Thin shell objects could now have more than one thickness.
SolidWorks also beefed up the software’s ability to do assembly modeling as well as its drafting capabilities. Although the software still had some aggravating problems and the on-line documentation left much to be desired, in the 14 months since SolidWorks first shipped, it had been improved substantially.
In fact, the rapid increase in functionality was starting to concern some industry analysts. Steve Wolfe covered this in the February 1997 issue of Computer Aided Design Report.
“.. as SolidWorks expands the capabilities of its software, it runs the risk of making it too complex for most designers to learn. That complexity might be all right for products that cost a great deal and are used only by experienced specialists, but it won’t do for a product that is attempting to broaden the base of three-D designers.
“A second question for SolidWorks managers and users to ponder is which functions belong in the basic product and which should be included in specialty applications. The addition of sheet-metal design is a good example. Not all products incorporate sheet metal. Adding sheet-metal development to the basic product makes it more complex. In SolidWorks 97, the sheet-metal design controls are simple and don’t get in the way. But as sheet-metal designers demand more automation, the complexity will increase and so will the user-interface clutter. If other manufacturing applications are added, the complexity of SolidWorks will grow geometrically.”[12]
Meanwhile, the war of words between Parametric Technology Corporation and SolidWorks was starting to heat up. As discussed in Chapter 16, Steve Walske, PTC’s CEO, did not feel that a real market existed for what was starting to be referred to as “mid-range” CAD solutions. At an analyst meeting in early 1997 Walske commented: “Low-end products are flawed because they can’t design a meaningful portion of the mechanical marketplace.”[13] That may have been true a few years earlier but by 1997, that was no longer the case.
Dassault Systemes acquires SolidWorks
In a move that surprised everyone not involved in the discussions, Dassault Systems announced on June 24, 1997 that it was acquiring SolidWorks for $300 million or about 12 times the company’s annual revenue. In a call from Paris late that night, Jon Hirschtick reminded me that in Engineering Automation Report’s first article on his company less than two years earlier, in October, 1995, I had written, “SolidWorks will have the most significant impact on the mechanical design market in nearly a decade.” Little did I expect that impact to come quite so quickly. There had been many acquisitions in the CAD/CAM industry during the prior 25 years, nearly all of which involved a company in trouble being acquired by a stronger player. This was one of the first that involved the merger of two strong companies. [14]
At the time of the announcement, SolidWorks had sold about 6,000 copies of its software. Several points concerning the acquisition were immediately made clear. First, and most important, SolidWorks would continue to function as an independent organization controlling its own product development strategy. Second, the SolidWorks package would continue to be sold by the existing reseller channel and not by IBM which sold the bulk of Dassault’s CATIA software. Third, SolidWorks would continue to work cooperatively with third-party software vendors. A decade later, this still holds.
The results of most acquisitions in the CAD industry have ranged from poor to terrible. Making an acquisition in order to increase the size of one’s customer base has generally proven to a mistake. Dassault’s acquisition of SolidWorks seems to have worked from the start because there was little market overlap between the two firms and Dassault proceeded to keep it that way. Dassault’s CAD business tended to be with large industrial concerns such as Boeing and Chrysler which had long term relationships with IBM as described in Chapter 13. SolidWorks customer base consisted primarily of smaller companies that flew under IBM’s radar. At the time, Dassault did not have a Windows version of CATIA which was the only platform SolidWorks supported. Also, there was not a mindset of competing with CATIA at SolidWorks since the company was more focused on Pro/ENGINEER and AutoCAD.
While there has been a moderate amount of technology sharing between Dassault and SolidWorks over the years, for the most part the two parts of the company have continued to go their separate ways. SolidWorks still uses the Parasolid geometric kernel even after Dassault acquired Spatial and its ACIS technology in 2000. Core business functions like financial management were centralized while customer-related activity including product content and direction was independently managed.
Competition with Autodesk
Early 1998 was also the start of a more aggressive marketing war between SolidWorks and Autodesk. In general, SolidWorks was on a roll, both technically and marketing-wise while Autodesk was struggling to rationalize its mechanical product strategy. Under Vic Leventhal, SolidWorks had built an impressive distribution channel with many of its resellers either former or current Autodesk resellers.
Autodesk announced in early 1998 that resellers authorized to carry Mechanical Desktop could not also sell competitive products, especially SolidWorks. Several major resellers including U.S. CAD and Micro Engineering Solutions were subsequently terminated by Autodesk.
About the same time, in February 1998, SolidWorks became a founding member of the OpenDWG Alliance (known today as The Open Design Alliance). The intent of this industry group was to provide software tools that facilitated the direct reading and writing of AutoCAD files using Autodesk’s internal DWG format.
Autodesk has never published a detailed description of the DWG format. As a result, programmers working under contract with the Alliance were forced to reverse engineer the file format. By joining the alliance, Autodesk competitors who wanted primarily to be able to quickly read AutoCAD files, could pool their development resources in this area and eliminate redundant development work.
Third-Party software key to SolidWorks strategy
For the next several years, SolidWorks delivered a new release of software about once a year. For the most part, the company focused on its core modeling and drafting technology leaving applications such as analysis, NC and PDM to third party vendors. As an example, even advanced surface geometry software was available from external sources. Aerohydro, of Southwest Harbor, Maine offered a program called Surface Works which had originally been developed to support the company’s ship design activities. Another example was Immersive Design, located in Acton, Massachusetts. Founded in 1995 by Greg Smith, Immersive offered an animation and visualization package called Interactive Product Animator or IPA as shown in Figure 18.3.
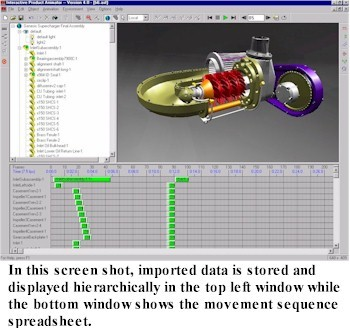
SolidWorks established its Gold Partners Program to facilitate the development of these third party applications. The intent was to provide a consistent look and feel between the applications and the SolidWorks program itself. As an example, CosmosWorks structural analysis software appeared to a user as simply an extension of SolidWorks. If the user wanted to rotate a FEA model, he/she used the same pull-down menu that was used to rotate a SolidWorks model. In this manner, SolidWorks was able to present its software and that of its Gold Partners as an integrated solution with a common user interface much like that of its larger competitors and of Dassault Systemes for that matter.
At NDES ’97, ANSYS’ demonstrated its new DesignSpaceapplication that wrapped their FEA program inside a SolidWorks compatible Windows interface. A fourstep “Will it break?” wizard simplified the analysis process for design engineers by providing a green flag (okay) or red flag (start over) as part of the process’ output.
Although SolidWorks had fairly good drafting functionality, the company signed an agreement with Adra Systems in April 1997 to add that company’s Cadra Drafting software to its list of supported third-party packages along with a customized version of Adra’s PDM package, MatrixWorks. A few months later Adra Systems split into two companies, the original Adra Systems that continued to market the Cadra drafting software and MatrixOne that took over development and sales of the Matrix PDM software. In 2006, MatrixOne was acquired by Dassault Systèmes.
SolidWorks becomes a serious design package
One measure of good software architecture is the speed with which a major package can be enhanced without adversely impacting performance or reliability. Watching SolidWorks evolve over the years seems to confirm the quality of its underlying architecture. With SolidWorks 98, released in early 1998, the company added numerous enhancements that facilitated the creation of complex geometry, drawing generation and assembly modeling. The latter area was a subject most CAD vendors were still struggling with, particularly in regards to the initial loading and display of complex assemblies. SolidWorks 98 was able to display a 150-component assembly almost instantaneously.[15]
By early 1999 SolidWorks had installed over 20,000 seats of SolidWorks and was starting to pursue deals in the 1,000 seat range. Although Dassault did not publish SolidWorks-specific financial results, Engineering Automation Report estimated that SolidWorks was doing $40 to $50 million on an annualized basis. The company established a major accounts team to go after these large deals. These teams were responsible for coordinating the activities of dealers, third-party software firms and hardware vendors in pursuing this business but the actual purchases were still directed through the dealers. SolidWorks worked hard to create a more positive business environment for dealers than what those companies experienced with other software vendors such as PTC and Autodesk.
The mid-1999 launch of SolidWorks 99 included a new three-dimensional sketching capability that facilitated the introduction of a new piping module priced at $995 per copy.
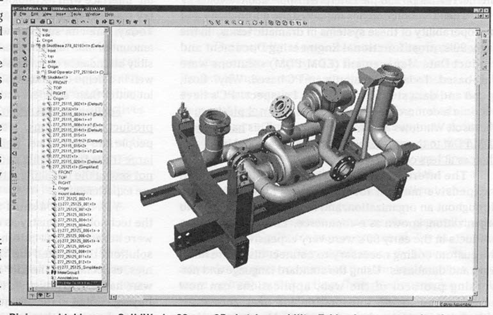
The company sold over 17,000 commercial seats of SolidWorks in 1999 for a total at the beginning of the new decade of about 43,000 seats. SolidWorks 99 was followed in early 2000 by SolidWorks 2000 with improved part modeling and drafting and speeded up assembly viewing. Users were particularly interested in improved assembly viewing speeds since the models being developed on these systems were getting bigger by the day and although computer power was also improving, much still needed to be done at the software level in order to keep assembly modeling from falling into disuse.
The one thing customers and prospects were not seeing was any effort to meld SolidWorks and CATIA, especially the new CATIA V5, into an integrated solution. Each system maintained its own development focus and sales appeared to target different segments of the market.
Management changes start
In the spring of 1999, Mike Payne, SolidWorks’ executive vice president of research and development became executive vice president of technology for Dassault Systèmes. R&D management at SolidWorks was split between David Corcoran who took over the development group in Massachusetts and Linda Lokay who was responsible for a separate development team in Cambridge, England.
About the same time, Dassault acquired a 75 percent interest in Smart Solutions, an Israeli company that marketed a PDM system called SmarTeam. This package was particularly well suited to users of SolidWorks although the two Dassault subsidiaries operated independently of each other. The SolidWorks version of SmarTeam was called SmartWorks.
By the end of 1999, SolidWorks had become a very comprehensive geometric modeling tool with decent assembly modeling capabilities. In less than five years since its first release, this software was comparable in many regards to more expensive software products that had been around for a lot longer. The company was now big enough to be the target of recruiting raids launched by a new generation of startups.
One example of this new maturity was a temporary restraining order SolidWorks obtained against Alibre, Inc. in March 2000. The order prevented the relatively new CAD company from recruiting additional SolidWorks employees. Prior to the restraining order being issued, Alibre had lured Tom Kopinski, former director of North American sales for SolidWorks, to be its vice president of sales. Kopinski, like other SolidWorks employees, had an employment contract with SolidWorks that prevented him from joining competitors. As mentioned earlier, SolidWorks had been involved in a similar legal case when PTC complained about SolidWorks poaching its employees. [17]
In mid-2000, Dassault purchased the solids modeling component software business from Spatial Technology including the ACIS modeling kernel. Many people expected SolidWorks to switch from Parasolid to ACIS since Parasolid was controlled by a competitor to both SolidWorks and CATIA.
eDrawings
Probably starting in the mid-1980s, CAD advocates proposed doing away with traditional engineering drawings and using model images and digital data for construction and manufacturing. Most of these pioneers were ahead of their times but gradually, drawings began to take a back seat to model data. By the late 1990s it was not at all uncommon for design groups to provide companies that were making dies, molds and other components with digital model data supported by a limited amount of twodimensional drawings. As an example, complex surfaces are very difficult to accurately define on an engineering drawing but easy to transfer from one system to another using either native data or industry standard formats such as IGES and STEP. But there was still a need for drawings, if only they could be made more useful.
In late 1999, SolidWorks introduced a new type of computer generated drawing the company termed “eDrawings.” As shown in Figure 18.5, an eDrawing was derived from a three-dimensional model, but rather than just containing two-dimensional data it carried with it the underlying model information. There were two versions of eDrawings, one which included the viewing software as part of the drawing file and one which assumed the recipient had the viewing software loaded on the computer on which the drawing was to be viewed. Obviously, the latter file was more compact.
SolidWorks provided both the viewing software and the software necessary for creating eDrawings free of charge although there was some consideration of charging for the publishing software known as eDrawings Professional. Eventually, the company expanded this capability to handle drawings generated by competitive systems including AutoCAD, Inventor, Pro/ENGINEER, Solid Edge, Unigraphics and Dassault’s own CATIA V5.
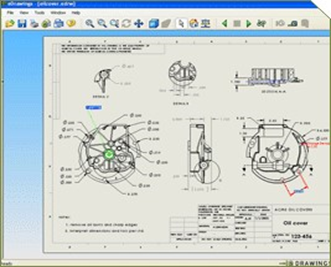
SolidWorks reaches maturity
SolidWorks 2001 probably defined a new level of maturity for this rapidly growing product. This release marked a new approach to the user interface that SolidWorks’ marketing people called “Heads Up User Interaction.” According to Engineering Automation Report:
“Following a trend begun in SolidWorks99, they’ve eliminated almost all dialog boxes. For example, when extruding entities, you can now assign values directly on screen, adjacent to the entities being extruded. The PropertyManager has now been implemented throughout the program, and context-sensitive callouts have been added. The latter appear within the model or drawing display to assist the designer. Context-sensitive callouts include symbolic sketch relation callouts as well as descriptive and editable feature callouts that display the appropriate design information, allowing the user to better understand and more easily modify designs. These callouts display information such as relationships on sketch entities, labels for feature inputs, or a method for changing feature parameters.”
By late 2001, Dassault’s acquisition of SolidWorks was looking very good. At a meeting held for the press and analysts at the company’s Concord, Massachusetts headquarters in November 2001, SolidWorks executives were pleased with what the company had accomplished and optimistic about the future. Depending upon how one evaluated the numbers, SolidWorks could claim to be the leading vendor in the mid-range three-dimension CAD market, exceeding the revenue in this segment claimed by Autodesk.
The underlying theme of the meeting was that the target markets SolidWorks was pursuing were far from saturated and that there was still a large pent-up demand for three-dimensional design software within design organizations that were still using twodimensional tools.
Hirschtick and other SolidWorks participants in the meeting emphasized that SolidWorks was basically a CAD company focused on producing the best design software possible and that it was not a PLM company. Sales in 2001 were running 20 percent above those of 2000 with 70 percent of the revenue coming from new customers. This was an exceedingly high number when compared to the competition. For example, 90 percent of PTC’s revenue was coming from its installed base.
SolidWorks claimed that 50 percent of its new business was coming from existing Pro/ENGINEER accounts. At this point, SolidWorks had sold over 160,000 seats of software, 88,000 to commercial accounts and the balance to educational institutions. By the end of the year, SolidWorks represented just under 20 percent of Dassault Systems’ revenue as compared to just 2 percent when it was acquired.
One of the major problems experienced by all software companies with a large installed base of users was how to determine where to invest R&D resources. User group wish lists and focus groups help but are not a complete answer. SolidWorks used an interesting software tool to help gather information from users. This tool could be optionally initiated by the user and about 5 percent of them had done so at this point.
The software collected information about what functions individual users executed, how often the software was active and problems the users incurred. This information was collected and sent to SolidWorks via email every two weeks stripped of any customer-specific data. One interesting statistic was that in 2001 each SolidWorks license was being used 550 hours annually compared to 450 hours in 2000. Not only were there more licenses in use, but each license was being used more intensely.[18]
A changing of the guard
A few days after the press and analyst meeting, the company announced on November 9, 2001 that its founder and CEO, Jon Hirschtick, had decided to step down.
John McEleney, formerly the company’s Chief Operating Officer, was promoted to the CEO position, effective immediately. McEleney was a five-year SolidWorks veteran who had built the company’s profitable partnership and subscription service programs and its Pacific Rim sales channel.
The change in leadership was not a complete surprise. For the prior three months Hirschtick had been on sabbatical and McEleney had been running the company. Hirschtick cited two factors in making his decision: personal and family concerns and a desire to position the company’s management team “to continue to achieve the phenomenal success that our company has experienced over the last eight years.”[19]
Hirschtick assumed a new role as group executive for SolidWorks at parent company Dassault Systèmes. He also continued in his role as a member of the board of directors of SolidWorks. Engineering Automation Report viewed this change favorably: “Our view on this is positive. Jon will remain involved with the company doing what he does best, which is providing guidance and vision. McEleney gets the title to go with the responsibility he’s had for a long time – he’s been doing an excellent job running the company and he deserves the CEO title. Jon gets to enjoy his children and focus on the long-term vision of the company. Everybody wins, especially the customer.”[20]
December 2001 also marked the introduction of SolidWorks 2001 Plus, the company’s tenth major software release. One significant addition was the use of Assembly Engineering Manager software from D-Cubed. The two companies had been working together to create software that would enable users to simulate true motion between solid components. SolidWorks 2001 also incorporated software that facilitated the design of assemblies where part mating conditions were critical to the operation of the product. There were also enhancements to drafting functions as shown in Figure 18.6.
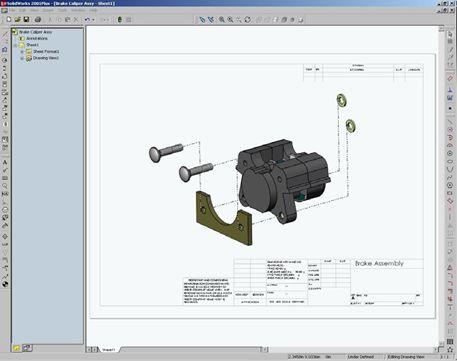
A major marketing strategy at SolidWorks was the need for users of twodimensional drafting software, particularly AutoCAD, to move to three-dimensional model-centric design. Until SolidWorks 2001 Plus, the company had not done much to help customers actually make the transition. SolidWorks 2001 Plus added several tools that facilitated the conversion of two-dimensional drawings into three-dimensional models. In effect, the user could place each two-dimensional view on the appropriate side of an imaginary glass box surrounding the implied three-dimensional model. A set of software tools could then be used to actually build the model from these views. One nice aspect of the software was as the model was rotated, the projected views moved with it.
SolidWorks jumps into PDM fight
By June 2002, it was clear that Dassault Systemes’ acquisition of Smart Solutions was not working out as well as the company had expected. Some of the SmarTeam employees were transferred to Dassault’s Enovia subsidiary, some to Dassault’s professional services organization and other to SolidWorks. Although the company continued to sell SmarTeam to users of other CAD solutions, the bulk of the effort became the responsibility of SolidWorks which began marketing SmarTeam through its existing reseller channel. It was clear that SmarTeam was the preferred PDM product for medium and large users of SolidWorks.
A substantial portion of SolidWorks installed base consisted of installations with just a few copies of SolidWorks. To meet the needs of these customers SolidWorks acquired a small private company, Design Source Technology, that marketed a stripped down PDM package called PDMWorks. It was inexpensive and fit the needs of installations with perhaps two to five copies of CAD software. It did not use a relational database manager such as Oracle or Microsoft SQL but, rather, maintained model and drawing data using the basic file management capabilities of the Windows operating system.
SolidWorks At Mid-Decade
In early February 2005, SolidWorks held its annual user meeting in Orlando, Florida with over 2,200 attendees. One sign of the impact the company was having on the CAD market was the fact that 77 companies had booths in the meeting’s exhibit area to show off SolidWorks compatible products. Also indicative of SolidWorks’ marketing presence was the company’s ability to have space pioneer Burt Rutan as the meeting’s keynote speaker. He described how he had built SpaceShipOne, the first privately financed manned spacecraft, using SolidWorks software among other design tools.
By mid-2005 SolidWorks had installed about 190,000 commercial licenses of its software and was generating about $225 million in annual revenue. SolidWorks’ revenue was over 21 percent of the parent company’s overall revenue and, apparently, an even larger portion of the company’s profits. Obviously, Dassault’s acquisition of the company in 1997 was proving to have been a wise move on the part of the French company. Dassault has continued to maintain a hands-off approach to managing the SolidWorks subsidiary. There is virtually no joint marketing of the SolidWorks and CATIA products and, in fact, there is only limited software available from the company for exchanging data between the two systems.
The total installed base was closer to 400,000 seats due to the company’s aggressive educational programs that provided schools with copies of SolidWorks at a steep discount. The company claims that over 700,000 students learn to use this software every year.
SolidWorks 3D Content Central has brought to reality a concept that many CAD pioneers dreamed about for years. Most products consist of some parts designed by the manufacturer and lots of parts procured from outside vendors. During design, dimensional data defining these external parts needs to be incorporated into the product model. Historically, this was a time-consuming manual task.
With 3D Content Central, parts suppliers are able to create SolidWorks compatible models of their components and post them on a web site managed by SolidWorks. Design engineers can download this data and incorporate the part information in the products they are designing. Nearly 100,000 parts were being downloaded per month in mid-2005 by SolidWorks users.
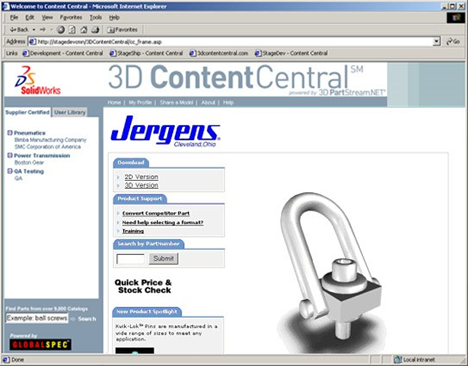
Another interesting development was the acceptance of eDrawing technology by non-SolidWorks users. Over 32,000 Pro/ENGINEER users had signed up to use this technology.
At this point, SolidWorks management consisted of:
- John McEleney – Chief Executive Officer
- Jeff Ray – Chief Operating Officer
- Joseph Esposito, Chief Financial Officer
- Chris Garcia, Vice President of Research & Development
- Bertrand Sicot, Vice President, North American Sales
- Dave Corcoran, Executive Vice President of Strategy
- Michel Gros, Executive Vice President, Europe
- Fuyuhiko Usui, President and CEO, SolidWorks Japan K.K.
- Ved Narayan, Vice President, Asia Pacific Operations
- Rainer Gawlick, Vice President, Worldwide Marketing
- Richard Welch, Vice President, Worldwide Customer Services
In July 2007, John McEleney announced plans to retire and Jeff Ray was appointed to replace him.