From first success to full transformation: how Sohbi Craft upskilled its workforce with Shapr3D
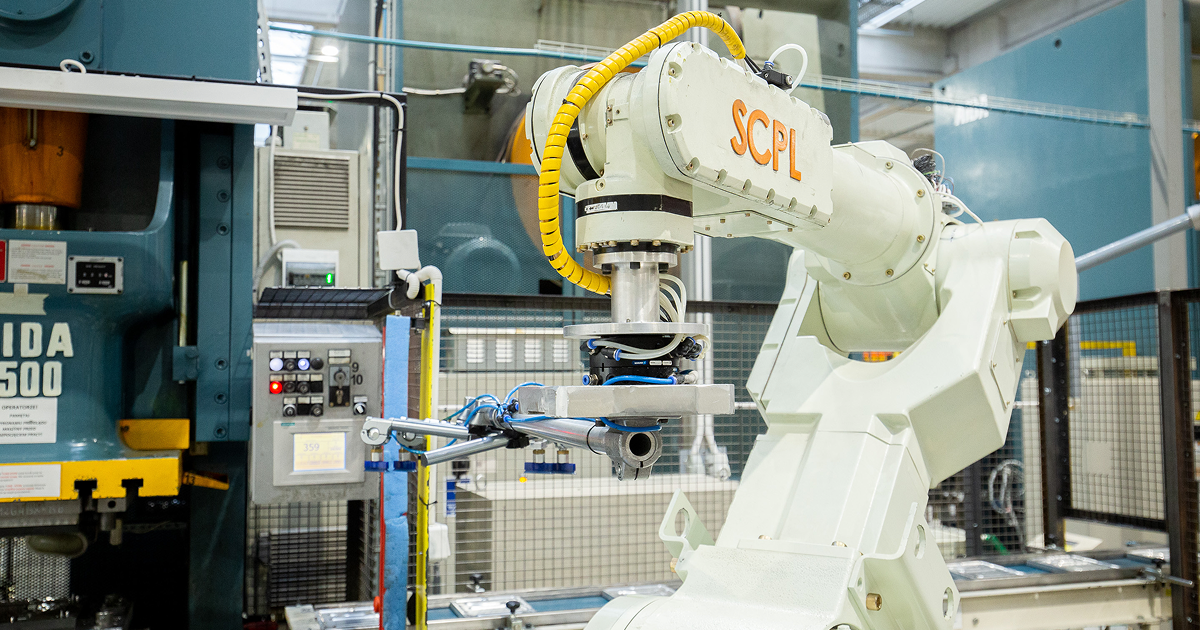
Key Outcomes:
- 40% faster production planning
- Saved up to 20 hours per project on equipment design
- €56,000 in internal cost savings in 2024
- €24,000 in revenue from external simulation projects
- Design capabilities expanded beyond engineers to technicians and robot programmers
Meet Sohbi Craft Poland
Sohbi Craft Poland (SCPL), a part of the Sohbi Group, is a global manufacturer specializing in precision metal components and industrial automation. Operating across Poland, Japan, and the Philippines, the company supports complex production needs for global OEMs.
In 2023, SCPL’s production engineering team was under pressure to innovate fast. They needed agile design tools to keep up with increasingly customized production lines and growing global demand. Enter: Shapr3D.
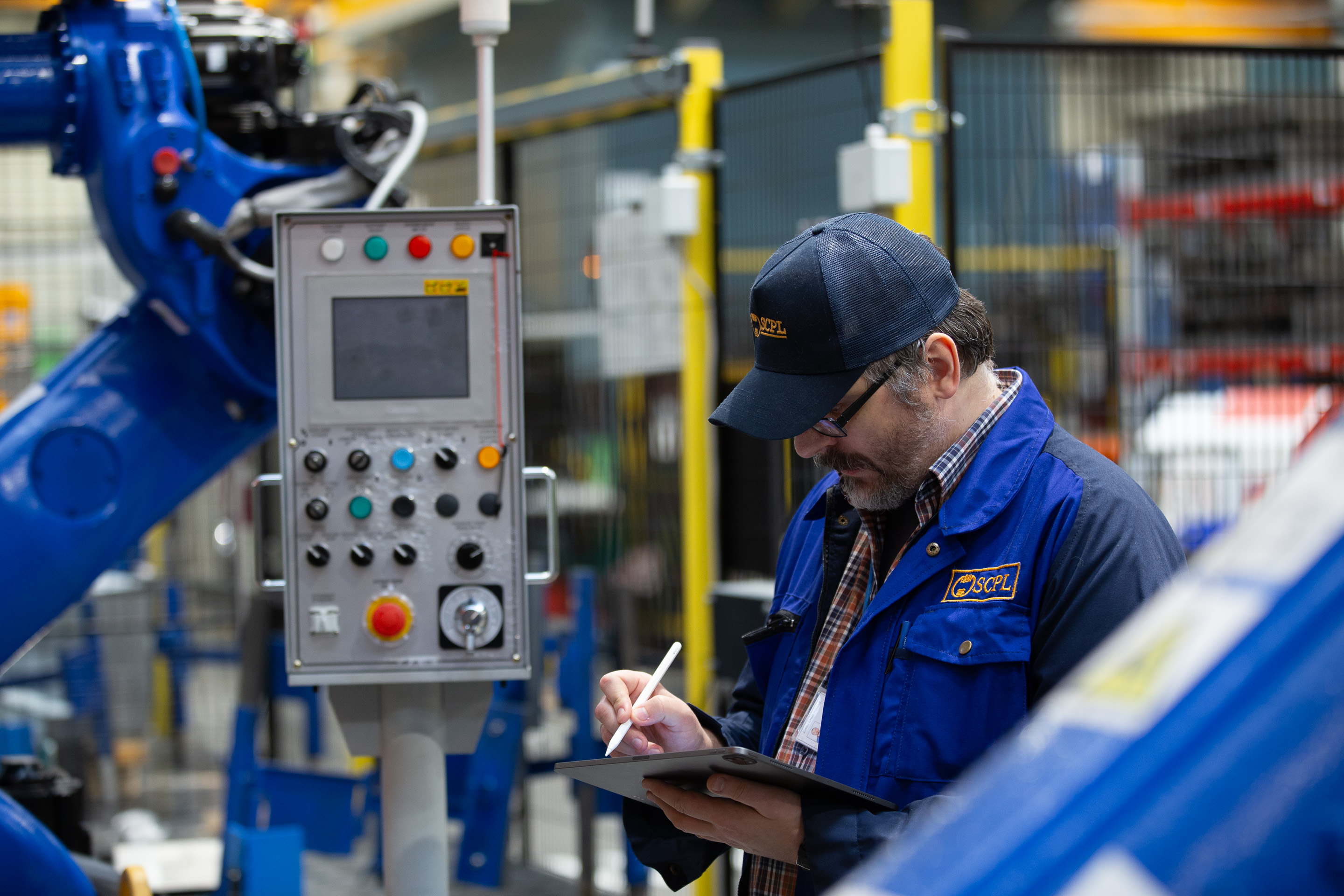
The first breakthrough: One engineer, one solution, one major win
The first milestone came when Marcin, an experienced production engineer with no prior CAD experience, used Shapr3D to design, simulate, and implement a complete production line in under four months—all without relying on CAD specialists or external resources. He modeled while traveling between sites in Poland, Japan, and the Philippines, using Shapr3D to communicate ideas clearly and visually to stakeholders.
His success proved something big: when CAD is accessible, innovation happens faster.
“I didn’t need training or help. I just opened the app, started modeling, and showed my ideas to people who immediately understood them,” Marcin explains.
That early win planted the seed for a much larger transformation.
From one user to a company-wide shift
What began as a single-user solution has since become a company-wide shift in how SCPL designs, collaborates, and trains. Today, Shapr3D is used daily by engineers, robot programmers, and technicians, many of whom had never used a CAD tool before.
“Most of the guys didn’t have much prior knowledge of CAD. They just started using it right away,” says Marcin. “Even people who hated CAD in school found Shapr3D easy and even fun to use.”
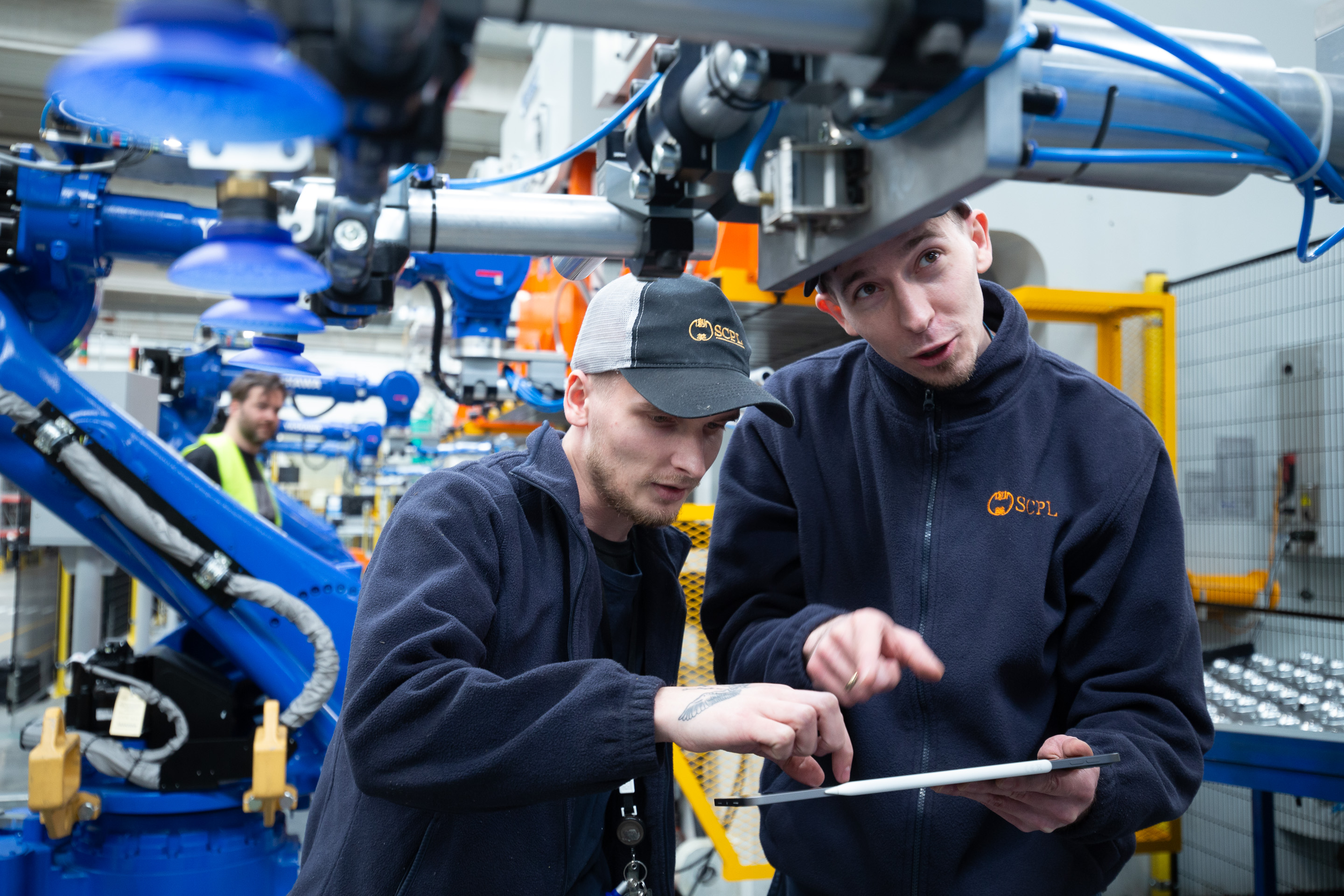
The team behind the change
Jakub and Szymon, industrial robot programmers, now design and optimize robot grippers using Shapr3D. They test ideas visually, speed up integration with production lines, and reduce downtime by iterating on the fly.
“Each product needs custom grippers. With Shapr3D, we design, test, and correct them ourselves. What used to take up to 20 hours now takes just 2–5,” says Szymon.
Grzegorz, another team engineer, collaborates with customers using Shapr3D to deliver production simulations, helping SCPL unlock €24,000 in simulation-based revenue in 2024 alone.
Arkadiusz, the Production Engineering Manager, oversees the entire team and credits Shapr3D with enabling more independent, confident work across the board.
Impact at scale with speed, savings, and shared understanding
As Shapr3D adoption spread, the benefits multiplied:
- Upskilled workforce: Design is no longer confined to CAD specialists. Technicians, robot programmers, and engineers create, modify, and share designs, making faster decisions and solving production problems on the spot.
- 40% faster production planning: What used to take days or even weeks now takes a few hours. Modeling in Shapr3D dramatically speeds up process design and planning, especially for new lines and automation equipment.
- Significant cost & time savings
- €56,000 in internal cost savings (2024), especially on simulation-driven production line modifications
- €24,000 in new external revenue for design and simulation services
- Eliminated wait times for external design requests (previously up to 20 hours per item)
- More inclusive collaboration: Shapr3D helped bridge communication gaps across departments. With shared 3D visuals, teams now brainstorm ideas together in real-time; no more lost-in-translation sketches or siloed 2D diagrams.
“We used to draw everything by hand. Now, we can see it in glorious 3D. It really changes how people collaborate.”
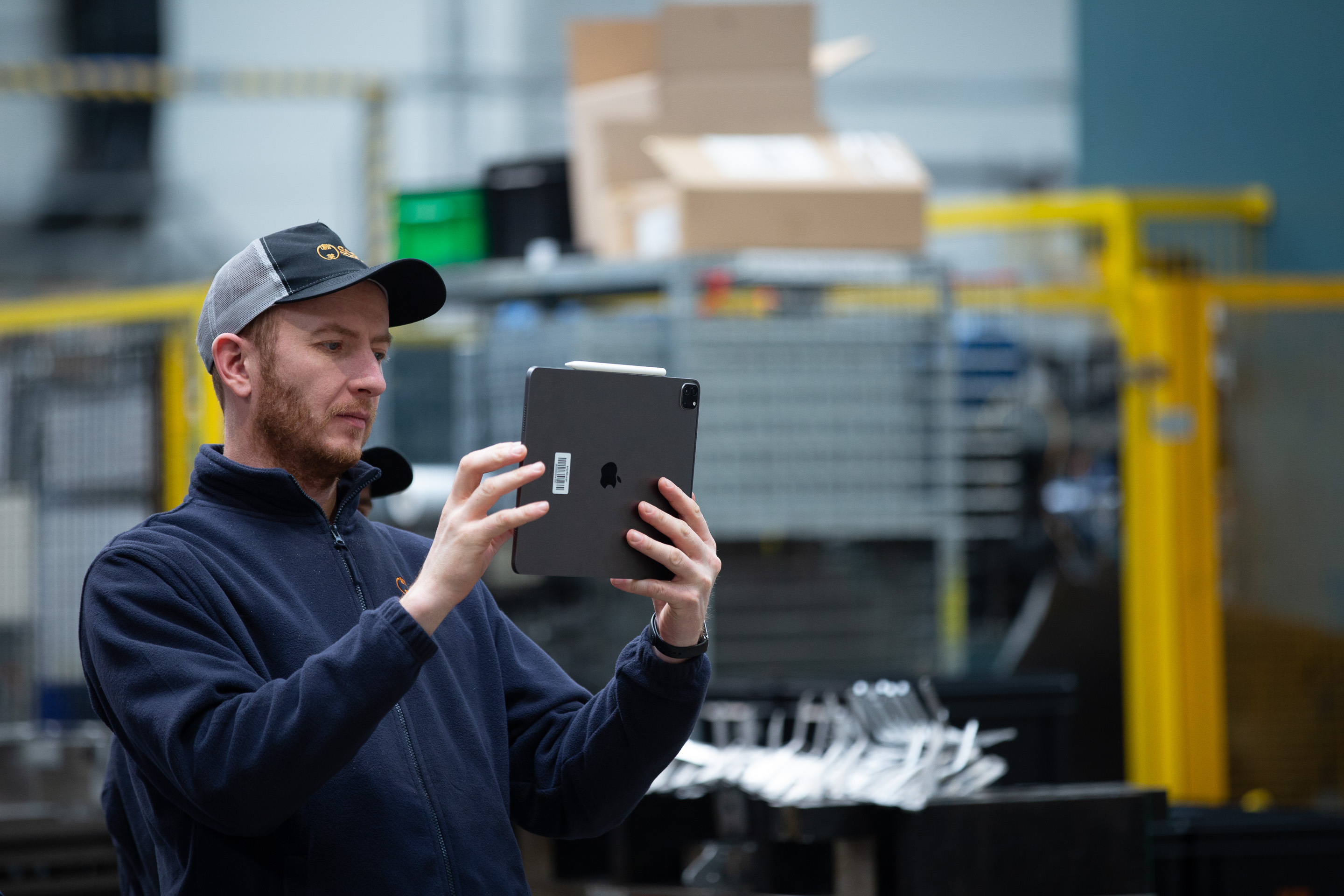
Inside the process
SCPL’s production line development involves Sales, Production Engineering (PE), Design, QA, and Logistics teams. Here’s how Shapr3D fits into the workflow:
- Feasibility check: The sales team assesses new production opportunities.
- Production process design: PE designs the workflow, creating models and plugging them into the simulation software.
- Gripper design: Each new product needs custom grippers, designed by robot specialists using Shapr3D.
- Approval & testing: Managers and specialists review and test the designs on actual lines, making quick adjustments as needed.
What’s next? A culture of continuous innovation
With Shapr3D at the core of its production toolkit, Sohbi Craft Poland is improving not just how it works but also who gets to create.
“The ability to create your own models quickly and efficiently—that’s the first step toward real digital transformation,” says Marcin.
Whether designing grippers, simulating new lines, or training the next wave of engineers, SCPL is proving that when design is accessible, progress becomes exponential.