Bridging design and maintenance: How 3M’s Kempten team streamlined prototyping and production with Shapr3D
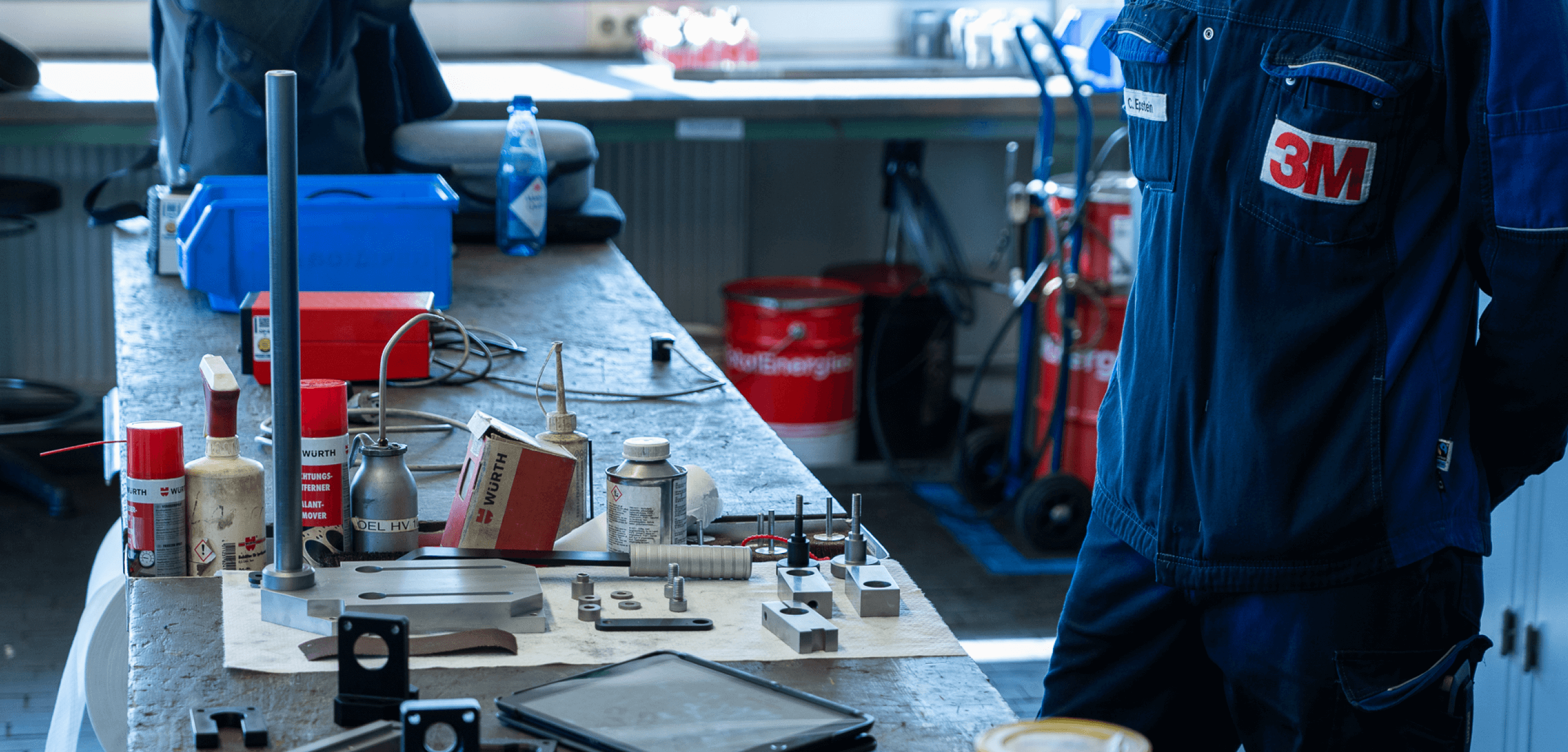
3M’s Kempten site in Germany isn’t your typical branch of the global science company. While many associate 3M with household names like Scotch, Post-it, and a range of safety products, the Kempten plant specializes in highly technical ceramic components, making it one of the only 3M facilities in Europe with this unique focus.
At the heart of the plant is Marcel, supervisor of the technical workshop. Since joining 3M as an apprentice in 2010, Marcel has moved through the ranks to lead a team responsible for keeping the site's extensive production infrastructure running smoothly.
“We’re a big plant with many different production steps,” Marcel explains. “We have specialists for pumps, ovens, and all kinds of machinery. My job is to make sure everything runs—or gets back up and running—quickly and efficiently.”
Communication breakdowns in the workshop
In a plant where technical complexity meets high-speed production, the team often faced a familiar but critical challenge: miscommunication. Requests for custom parts or repairs would arrive in the form of vague hand sketches or verbal descriptions.
“Someone would come to us and say, ‘Hey, we need this,’” Marcel recalls. “They might come back an hour later and say, ‘Oh, I forgot—can you change this or that?’ You end up calling them back, measuring again, clarifying, or even restarting the job.”
This process didn’t just slow things down—it introduced risk at multiple points. The team often designs jigs, fixtures, and custom equipment to hold or guide parts during testing or production. But when these requests came as rough hand sketches or verbal descriptions, important details were easily lost. As the designs moved from engineer to machinist to apprentice, the chance for errors compounded. “Everyone thinks they know what the sketch means, but by the time it gets to the person operating the machine, it can be totally misunderstood,” says Marcel.
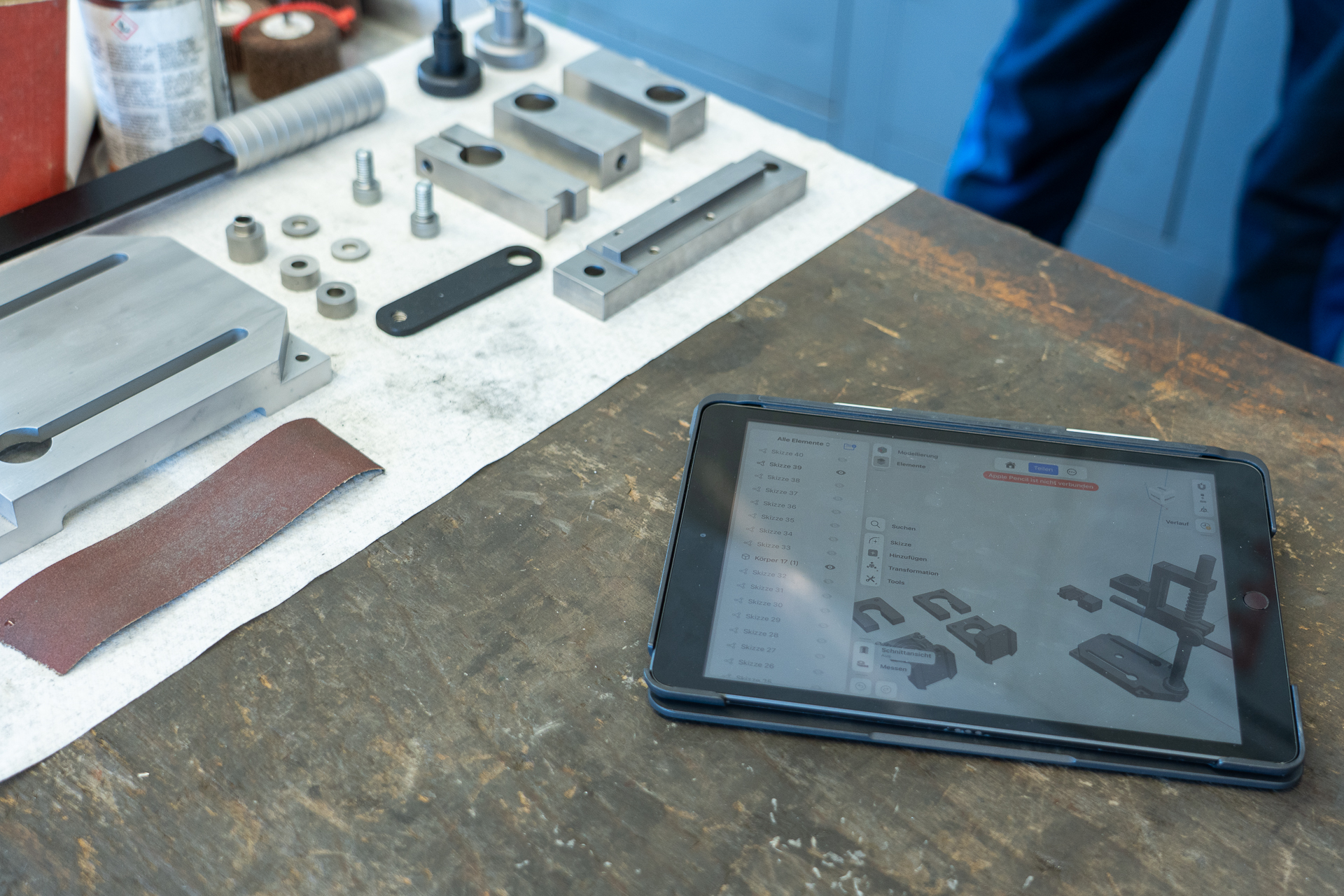
From concept to prototype in minutes, not weeks
One of the most powerful examples of Shapr3D in action came from the R&D department. Researchers needed a custom part to test how powders flowed through different channels. In the past, this request would have taken weeks of back-and-forth.
“Instead, we just jumped on a Teams call,” Marcel recounts. “While they explained what they needed, I opened my iPad, launched Shapr3D, and started modeling in real time. They saw the design as I built it.”
Once confirmed, the part was quickly sent to the CNC machine for prototyping.
“Before, this would take four to eight weeks. Now it’s same-day,” says Marcel.
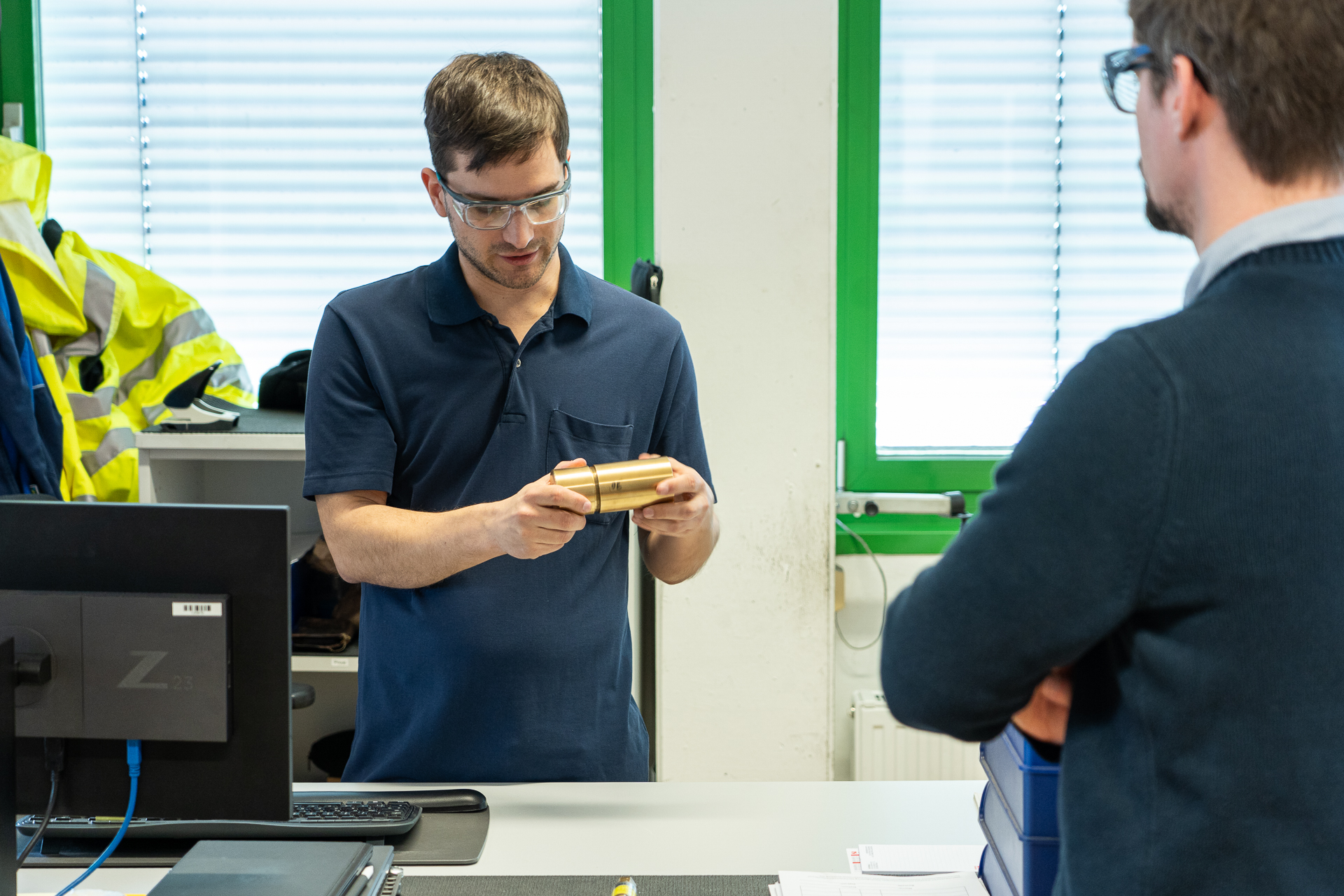
3D printing becomes a reality
Shapr3D didn’t just speed up communication—it made 3D printing a practical tool for the maintenance team for the first time.
“We had a 3D printer, but no real way to create usable models for it,” says Marcel. “Tools like Inventor were too complex and slow for our team. No one in maintenance really used them.”
That changed with Shapr3D, and 3D printing became part of the team’s daily work. Its ease of use gave them the confidence to start designing in-house. “Before, a simple part might take four hours to model in other software. With Shapr3D, it’s done in an hour, and I can print it the same day,” adds Sebastian, a mechanic who manages printing at the site.
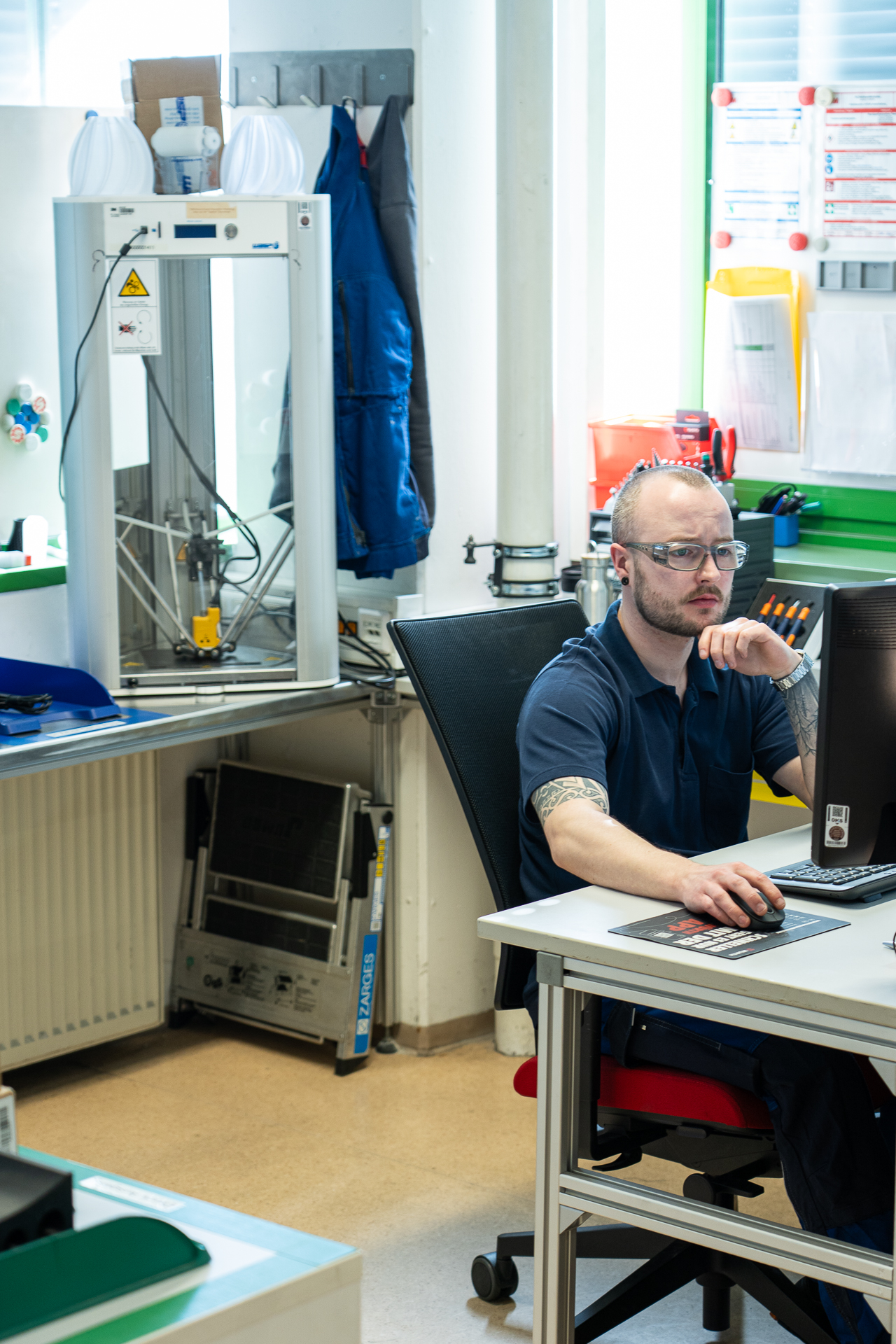
A new workflow takes hold
Getting started with Shapr3D was surprisingly easy for the team.
“I just hand over the iPad and say, ‘Do the clamp holder tutorial.’ In 20 minutes, they’re up and running,” says Marcel.
The app’s built-in guides helped everyone get comfortable with 3D modeling fast.
Once the team got going, their whole workflow shifted. “We now start with a sketch right in Shapr3D,” Marcel explains. “It’s quick to create, easy to update, and much more precise than a hand sketch or verbal explanation. “With this, we plan ahead more. It makes the manufacturing process much smoother,” says Marcel.
Scaling the impact across the plant
So far, the biggest adopters of Shapr3D are in the maintenance department. But Marcel sees a much wider opportunity. “I did a small showcase for other engineers, and they were impressed. If we can get more of the planning team and technicians to use it, it would have an even bigger impact.”
Some engineers have already started sending Shapr3D models instead of paper sketches. “That’s exactly what I hoped for,” Marcel says. “We used to get vague descriptions. Now we get solid, shareable designs.”
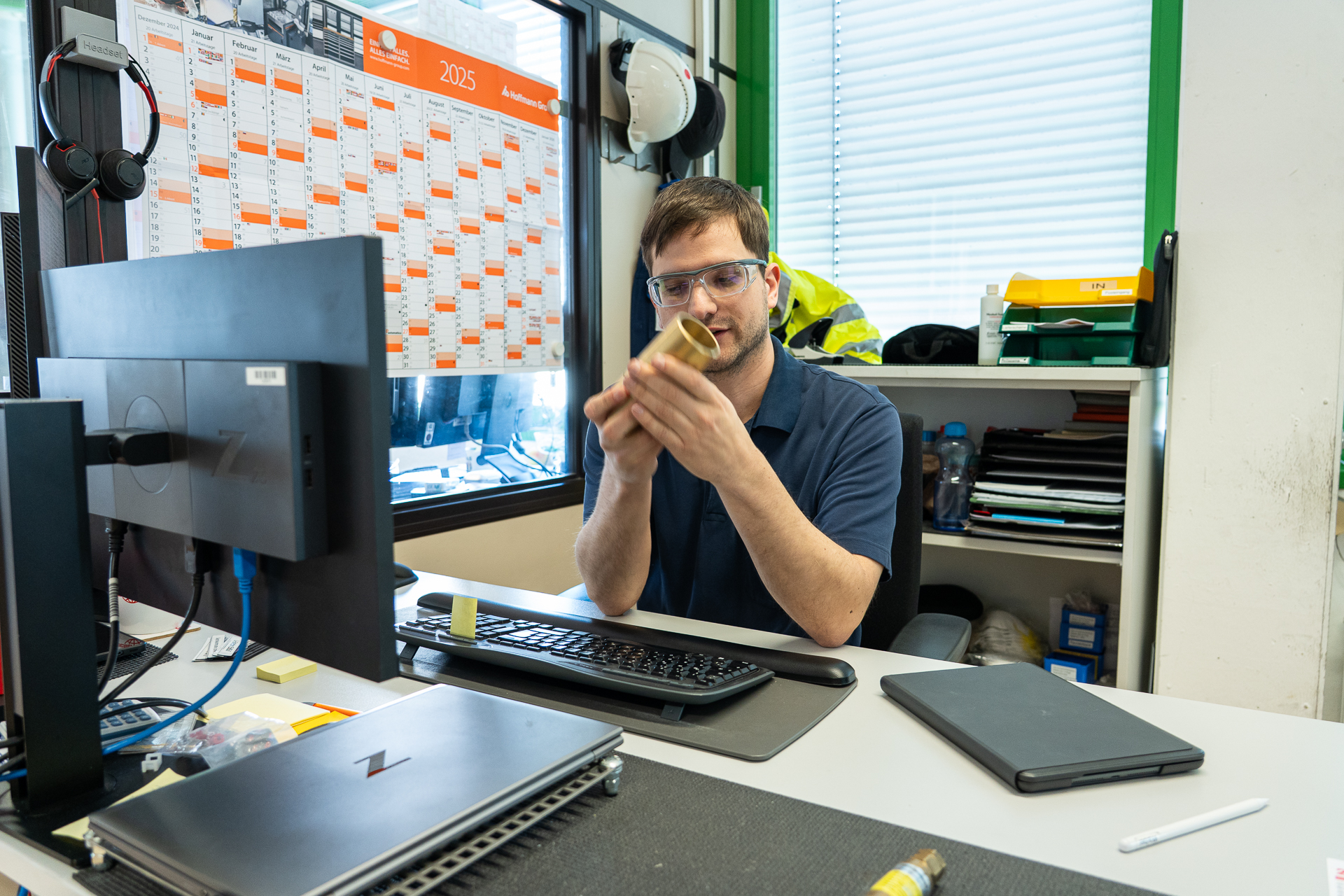
Looking ahead
The success of Shapr3D at 3M Kempten is a testament to bottom-up innovation. What started as a hobby tool became a central part of a highly technical production workflow—bridging communication gaps, reducing lead times, and enabling the team to expand into 3D printing.
“We’ve come a long way,” says Marcel. “And we’re just getting started.”