3D printed jigs and fixtures
.webp)
Jigs and fixtures are pivotal in creating a solid foundation for the overall manufacturing process in order to maximize productivity while ensuring worker safety and cutting costs. 3D printing as a form of additive manufacturing (AM) is a complementary method that can achieve these same aims with its implementation.
3D printing and effective jigs and fixtures manufacturing have overlapping aims which, when combined, directly complement each other.
While 3D printing went through a revolution in the 1980s, it wasn’t until decades later in 2020 that its credibility was fully realized during the height of the COVID pandemic. As hospitals scrambled to safeguard staff and patients alike using personal protective equipment (PPE), many turned to 3D printing to manage the shortage. This shift in verifying the practicality of 3D printing was also supported by overall growing trends in the use of 3D printing. In 2019 the use of 3D printing in additional sectors, specifically manufacturing, had skyrocketed, jumping from roughly 24% in 2016 to 65%. As of 2021, 57% of manufacturing companies used 3D printing for tooling and producing jigs and fixtures as compared to 37% in 2019 and 30% in 2017.
A comprehensive look at the benefits of 3D printing, adoption limitations, commonly used materials, and jigs and fixtures production best practices can shed light on the degree of effectiveness of integrating 3D printing into jigs and fixtures manufacturing.
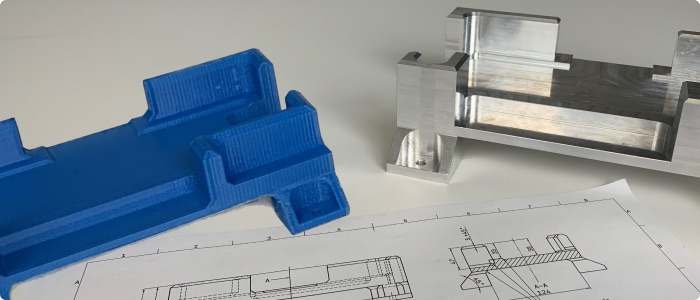
Additive manufacturing, or 3D printing, consists of constructing an object in parts, layer-by-layer, from a Computer-Aided Design (CAD) model. Conversely, traditional manufacturing methods include subtractive manufacturing (SM) and formative manufacturing, with CNC milling, drilling, grinding, or molding techniques being the most common. Subtractive manufacturing entails removing the final product from a larger form of material, producing waste with each product manufactured. Both methods require skilled training for professionals, significant time investment, and more expenditure.
3D printing jigs and fixtures is a practice being incorporated by a range of companies from the automotive industry to the medical industry. When it comes to making a return on investment, how does 3D printing measure up? Below are some of the highlights of how using 3D printing can be advantageous, specifically in the production of jigs and fixtures.
Faster production
The flexibility of 3D printing helps to increase productivity. This is due to the ability to iterate and rapid prototype while using fewer parts to create the final product. The minimization of error also contributes to increased productivity. Jenika Bishop, senior project engineer at Polaris Industries in India cites the shorter wait time for in-house production of 3D products as a significant factor in overall productivity. “Instead of waiting between eight to 12 weeks, we’re able to get designs within 24 hours,” he states (Schwaar). The ability to concept a design within a short span of time helps to close in fast on a final product to then order the right part in bulk if outsourcing is still the best option.
Design flexibility
With the ability to print multiple iterations of a product on the same day, products can be easily adjusted and customized as needed. Complex shapes that otherwise would be challenging to execute accurately using subtractive or formative manufacturing, can be created more freely using the layering technique of additive manufacturing. Waldemar Hirsch, 3D team project manager at Audi R8 Factory in Berlin highlights the company’s ability to automate the pre-assembly fixture production process with the application of 3D printing. “That allows us to make the necessary tools quickly and flexibly and to respond to specific requests from the planners or our colleagues on the assembly line.” (Schwaar)
Freeing up resources
The minimal need to supervise 3D printing once it starts on the machine frees up time and resources to work on other tasks, creating an opportunity for additional high-value work.
Reduction of cost
Beyond the initial investment of 3D printers, costs are reduced in several ways when using 3D printing. The reduction of waste by creating only the final product from the start cuts spending on materials that will become useless byproducts. While outsourcing parts production can increase costs both by the added labor costs and the shipment costs to receive parts, converting production to occur largely in-house can minimize overall expenditure significantly. Prototyping with AM cuts costs significantly as opposed to prototyping with more expensive processes such as CNC machining.
The shift from using 3D printing as a cutting-edge sculpting tool to its recognition as a manufacturing tool has resulted in a number of advantages with its growing popularity as a mainstream option. As 3D printing matures, considering its relevancy in its current stage can help to make an informed decision about if and when to plan to implement it in a manufacturing workflow.
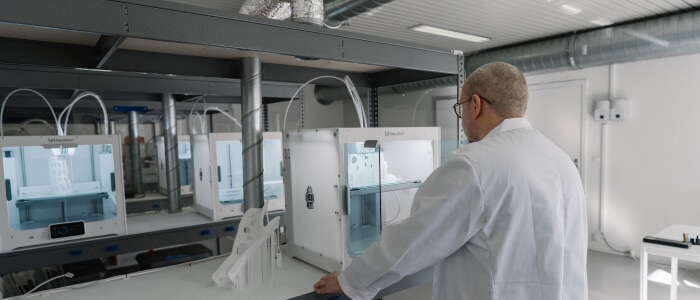
Initial investment
As of 2019, 87% of companies considering adding 3D printing to their manufacturing operations were hesitating due to the high cost of machines. The cost of production-level printers ranges from roughly USD $5,000 - USD $1,000,000 while the cost of materials varies for polymers, elastomers, or metallic feedstock such as powder, resin, or wire. For jigs and fixtures production, in particular, the likelihood of meeting and exceeding a return on investment (ROI) in a shorter period of time is increased due to the quick production involved.
Limitations of technology
The end-product size, materials needed, and overall quantity of production are all considerations in whether 3D printing can be implemented effectively to save time. The specific use case of jigs and fixtures production exceeds most technology limitations due to the smaller size and lower cost of materials. For instance, 89% of time savings were reported by Volkswagen Autoeuropa in Portugal after implementing 3D printing for jigs and fixtures manufacturing .
Business challenges
Logistically integrating 3D printing for jigs and fixture production involves planning ahead to ensure seamless vertical operations integration. While opting to increase self-reliance by keeping jigs and fixtures in-house versus outsourcing can bring significant savings in both costs and time, the move also necessitates additional initial expenditure. This backward integration can affect a company’s long-term flexibility if not adequately prepared. If strategized effectively, the investment is more than made up for with the return. Rellan Martinán Martinez of Nissan in Barcelona, Spain reported in 2014 that the automobile plant was spending 20 times more in outsourcing than by turning in-house to 3D print the parts they needed (Schwaar).
While 3D printing jigs and fixtures is often better compared to traditional methods, it's not always the case. The below considerations should help you decide if this if it's the right option for you
Complexity of product
While the innate process of 3D printing a product in layers allows for more complex products to be printed directly with minimization of waste and simultaneous precision, the method reaches its limits with intricate pieces. The manufacturing of very complex products is better served with traditional manufacturing methods that have a history of development specific to producing particular types of products. For products that have a high degree of complexity without being very intricate, additive manufacturing can eliminate additional processes such as forging and joining, essentially providing the production of complex products “free of cost.” The low complexity of jigs and fixtures makes it an ideal product for utilization in additive manufacturing.
Customization
The agility of the process of 3D printing lends itself to effectively producing custom products. Quick iteration and editing at any point during the design and manufacturing process make pivoting in a design concept simple.
Volume
The limitations of 3D printing at its current stage of maturity make it less ideal for the large-scale manufacturing of more complex products.
The availability of materials specific to printing jigs and fixtures has evolved and expanded to ensure increasingly higher-quality end products. Typically, 3D printing utilizes a range of materials including molten material, liquid resin, and discrete particles, among others, which are often combined in 3D printing. Below are highlighted a few of the most common materials in 3D printing jigs and fixtures.
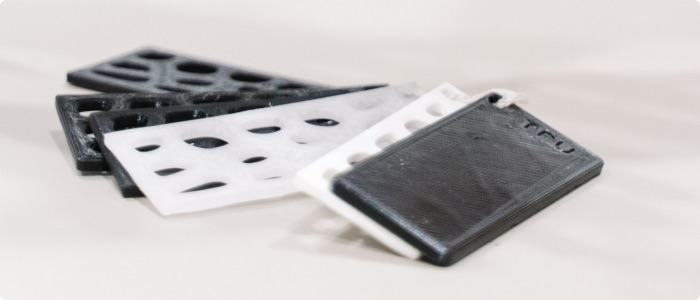
ABS (Acrylonitrile butadiene styrene)
Typically the most popular product for 3D printing, ABS is also the material of choice for jigs and fixtures production. This is due to the overall durability and strength as well as low cost. Cooling, when printed, is not recommended due to the high melting point that can warp the material when cooled suddenly.
Polyamide (Nylon)
Nylon exhibits high ductility and durability ideal for producing responsive prototypes. Its heat resistance as well as toughness with partial flexibility make it ideal for snap-fit components. This material is more expensive than ABS.
PLA (Polylactic acid)
PLA is a biodegradable plastic that is plant-based and is one of the most common materials for 3D printing given its versatility. For temperatures below 50 degrees Celsius, it is ideal for providing strength and stiffness for a product. Overall, PLA is very user-friendly and can be used with most print settings.
Reinforced fiber
Reinforced materials such as carbon fiber or nylon reinforced with fiberglass can provide more durability for longer performance.
ESD resin
ESD (electrostatic discharge) resin is a commonly used material by manufacturers for its cost-effectiveness and to increase production on electronics manufacturing lines. ESD materials overall discharge static, helping to protect parts. ESD resin is strong and durable, making it optimal for production.
While integrating 3D printing into your manufacturing process you need to consider some best practices and workflow planning that we've listed below.
Best practices
When it comes to designing your jig or fixture you do need to be careful. As with traditional manufacturing methods, 3D printing also requires attention to get it right. We've outlined some best practices below, and we also recommend reading our full in-depth guide on how to design for 3D printing.
Prevent warping
To avoid part deformation, or warping, that can occur with sustained loading over time, make sure to close the build chamber.
Plan ahead for complexity
Building complex aspects of a part or including engravings in a model ahead of time can help to quickly produce the product needed. Many of these processes would require additional steps with traditional manufacturing but these can be minimized or eliminated when using additive manufacturing.
Testing
Adding geometrically accurate references, or a datum feature, directly into the build of jigs and fixtures helps to check their functionality and avoid errors in production. Performing consistent testing to check the reliability and performance of a prototype can reduce lead times for bringing the product to production.
3D printing workflow planning
Alongside some best practices, you'll also need to consider how your 3D printed parts will fit into
Assembly
Mastering the process of securing as well as ejecting parts in the workflow can ensure high productivity. By printing lightweight parts, both become easier due to the lower weight of the part. Consider printing other parts needed to supplement the manufacturing process such as work-holding devices and guides.
Design for anticipated use and environment
By taking into account how a tool will operate to form the product supported by a jig or fixture, a jig or fixture can be designed more accurately to support the entirety of its use case. More space in sections of the jig or fixture could allow for the full range of movement of the tool or any waste material such as the accumulation of dust created in the process. The material used also needs to fit the conditions of the environment, taking into consideration heat, cold, or chemical exposure.
Worker experience
While 3D printing jigs and fixtures helps to minimize human error and protect workers’ safety, additional improvements can be made by designing the fixture for single-hand use or for secure holding by another machined part. Jigs and Fixtures can also be customized for an individual task.
Optimizing the 3D design process can further bolster productivity in 3D printing jigs and fixtures.
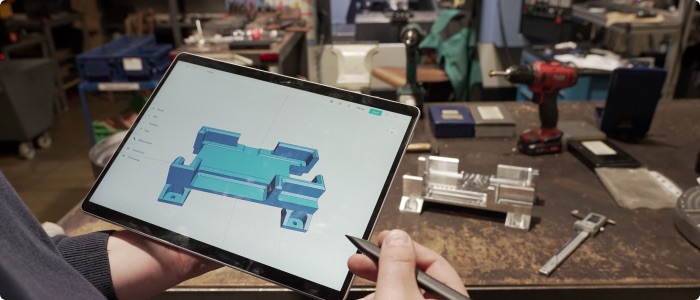
Since CAD software differs in providing either a parametric or direct modeling approach, it is important to pick CAD software based on the product needed. For rapid prototyping, direct modeling is the most time-efficient method due to the speed of concepting and ease of editing. Direct modeling allows for the design to occur by interacting with the geometry of the model, pushing and pulling as simply as molding clay. The method is also more simple to learn, meaning that professionals can use CAD without needing to attend training or have any past CAD experience.
Shapr3D enables for fast modeling with the freedom to go from concept to product in a matter of hours. When you design, a set of tools pops up on the screen to match your design process so you can select your next tool without having to search for it in a clunky menu. Consistent milliseconds of time-savings add up to cut overall design time significantly while enabling you to give your full attention to your design for more focused problem-solving and creativity.
This combined with the ability to learn Shapr3D in minutes breaks down any intimidation around designing with CAD for a seamless, guided learning process. The software also lets you design from anywhere you want so you can shift between working on desktop to making edits right next to your machine.
Though 3D printing evolved gradually and its appearance in the mainstream at the start of this decade seemed sudden, the method is predicted to further cement itself into manufacturing at large.
The same organization that in 2011 forecasted the occurrence of the COVID pandemic and societal shifts in behavior with the use of masks, also foresaw the cementation of 3D printing as a viable manufacturing option. The Institute for the Future released its report on The Future of Making in 2008, documenting the emergence of 3D printing in a decade as pivotal in addressing future changes in societal needs, specifically in addressing a potential disruption in the supply chain. In 2011, New York Times called 3D printing, “manufacturing’s Big Bang.”
Similarly, current research shows the advent of using 3D printing not just for rapid prototyping but for rapid tooling and direct manufacturing overall. The diversity of the application of additive manufacturing across industries along with materials and methods continues to expand, paving the way for a decade shaped by the immediacy and accessibility of 3D manufactured parts and products.Jigs and fixtures are pivotal in creating a solid foundation for the overall manufacturing process in order to maximize productivity while ensuring worker safety and cutting costs. 3D printing as a form of additive manufacturing (AM) is a complementary method that can achieve these same aims with its implementation.