3Dsystec team breaks down communication & workflow barriers with Shapr3D
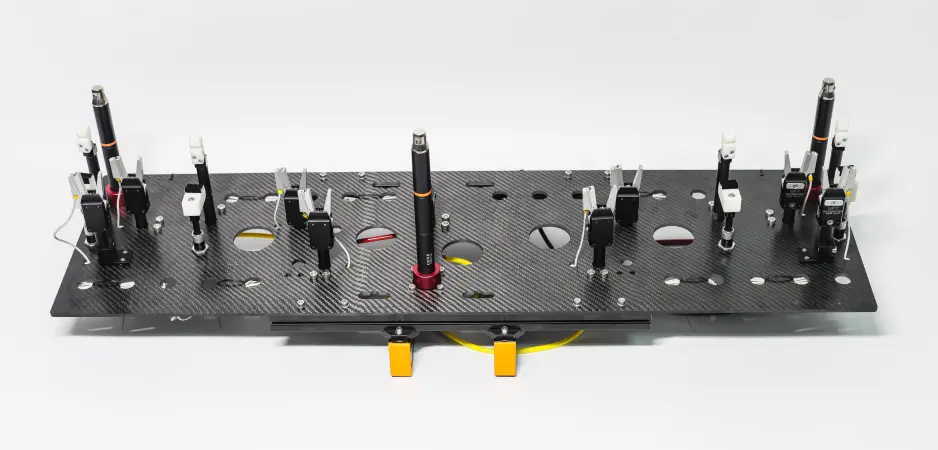
Overview
Hong Kong-based enterprise, 3Dsystec, delivers a ready-made infrastructure for its clients by offering end-to-end tooling delivery. With China as a whole ranking #1 globally in the machine tool industry, teams aiming to compete and thrive need to collaborate effectively and increase workflow flexibility. Amidst the larger global shift to production automation to address the currently smaller workforce, 3Dsystec has the potential to meet the rising demand for its services.
Recently, 3Dsystec has revisited how to optimize its team workflow to both communicate more effectively and innovate machinery used on location. With minimal barriers to communication and less confinement in their workflow, the team is poised to increase productivity.
About 3Dsystec
By delivering process simulation, project management, process engineering for injection molding processes, and building end-of-arm-tooling (EOAT), 3Dsystec provides comprehensive tooling and molding delivery. The Hong Kong-based company provides its clients with the necessary tools and processes to implement building their final product themselves. This benefits their global clientele with 90% coming from automotive manufacturing companies such as BMW, VW, and Tier 1 suppliers.
The CEO/CTO and tooling manager, Wolfgang Bregenzer manages a team of 22 including project engineers, CAD designers, and measurement engineers along with sales and accounting. The team also works with external manufacturers to complete the final product. Wolfgang and his multi-faceted team use Shapr3D to strengthen internal and external communication in order to support production and delivery.
Challenge
- Modeling on a laptop inhibits mobility and is cumbersome
- Mistakes in communicating data & measurements can be costly
- Inaccessible CAD limits team problem-solving & productivity
Solutions
- Boost in-transit & work floor productivity with quick access to multi-device design tools
- Communicate in 3D with modeling tools to clearly show design intent
- Cut production time with accessible 3D design tools
Why Shapr3D
Wolfgang started out traveling for client meetings with a 15” MacBook but found the process of modeling cumbersome. Feeling constrained by the weight and tediousness, he bought his first iPad and downloaded Shapr3D. The switch enabled him to create 3D data for note-taking and review models from his team.
Reviewing part models while traveling internationally to see clients in Europe, Canada, the United States, and Mexico was now a smoother process. At first, Wolfgang only used Shapr3D to view and check plastic parts. Now he and the team find the multi-device capability and short learning curve enables more effective communication and acts as a tool to maximize their professional skillsets.
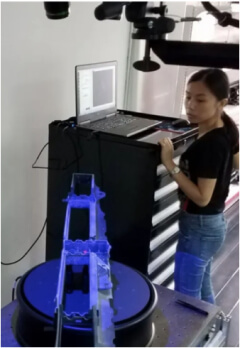
Multidevice CAD workflow improves transparency for project management
Traveling to meet clients means Wolfgang is often on the go and needs the ability to manage projects effectively while in transit. Previously, this meant sacrificing productivity in his workflow because the weight and size of his laptop made it inconvenient to access his work.
Now using Shapr3D on his iPad, he’s able to review parts and sketch out concepts by simply snapping open his iPad and storing it quickly when on the move. He’s found it very easy to rotate models to see from all perspectives to accurately assess them. This enables him to maintain oversight of projects even when he’s not present at the office.
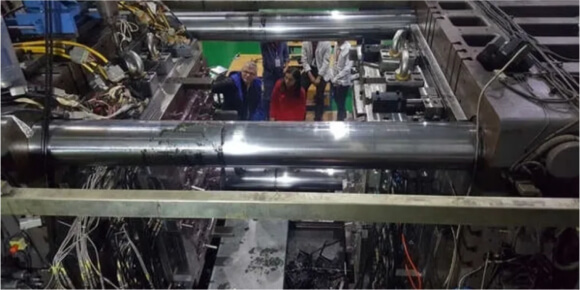
“It’s very easy to create shapes and some basic geometry. I don’t need to go into detail with the shape. I just make a rough sketch so that [the designer] can see it. Then I give it to our designer and let them do it that way.”
Though at first Wolfgang was the sole team member using Shapr3D on his iPad, now the team is equipped with five iPads. And how have they started using them? Wolfgang says that recording data on the work floor helps to minimize mistakes. Previously, the team took measurements while on the floor and then walked back to their offices to record the data.
Drafting models and recording measurements on the spot now helps to cut down on development time and streamline effort. If a team member notices a mistake, they can correct it immediately using Shapr3D. Anyone on the team, from engineers to Wolfgang himself, can check and review parts on the fly using Shapr3D on iPad.
Equalizing communication & working together to streamline production
With a small team working closely together across diverse professional and national backgrounds, using Shapr3D has been an equalizer in communication. Collectively, the team uses English to communicate but it’s a second language for all of them. Given the complex processes the team undertakes, instinctive CAD has become a vital visual mechanism for strengthening communication.
This has further minimized mistakes, helping to boost productivity. For injection molding parts, Wolfgang can make a simple sketch to show a rough volume to his team, suggest where to make a cut, and they can immediately act on his idea. 3Dsystec sales representatives can also clearly communicate designs to clients using Shapr3D Visualization and Review Links.
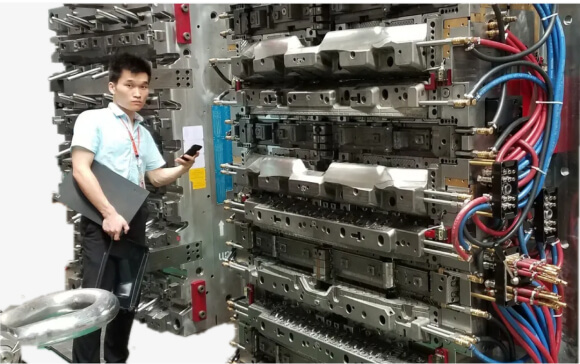
Systematizing innovation with instinctive CAD
With Wolfgang and the design engineers able to quickly express and model concepts, they’ve been able to better utilize their individual professional skillsets to problem-solve and boost productivity. As a tooling manager, now Wolfgang has expanded from reviewing models.
Using instinctive CAD software, he can channel his existing skills into creating tooling models that improve the team's design workflow. Likewise, the team can funnel their specific area of expertise, such as engineering or sales, into problem-solving more efficiently using 3D design. Most recently, Wolfgang created a model for an EOAT that was prototyped on a small scale. With the model deemed successful, the team manufactured the EOAT at five times the original scale for regular use in the workshop.
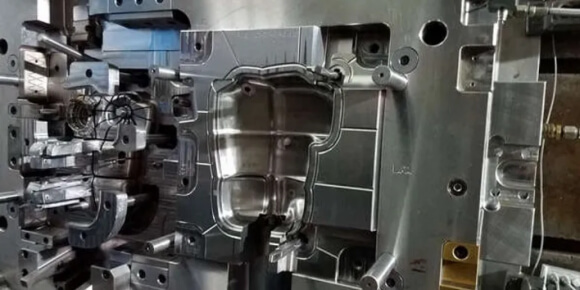
What’s next for Wolfgang and his team? He is currently experimenting with using carbon fiber tubing to create a system of EOATs. This innovative step means that the team can increase speed, quality, and precision while cutting costs. To design the system, Wolfgang is drafting the concept in Shapr3D to create full-fledged models for initial prototyping. In the past, Wolfgang was an outsider to the design process. Amid a tight labor market, equipping the team with an instinctive CAD tool increases the team’s overall potential for productivity, helping to offset any labor challenges while rising to the increased demand for production automation.
“My workflow changed a lot. It’s a lot easier to explain, to show ideas to people, to give ideas to people. At the moment, I’m creating a system of making EoATs completely from carbon. I designed this completely in Shapr3D. This is a process over the next two or three months. Before it was impossible to take my computer everywhere. Now I can sketch out my ideas while sitting on my sofa at home. Then the next day [the engineer] can make changes. This is a very big advantage and very easy to use.”