How manufacturing teams are closing the communication gap with 3D design
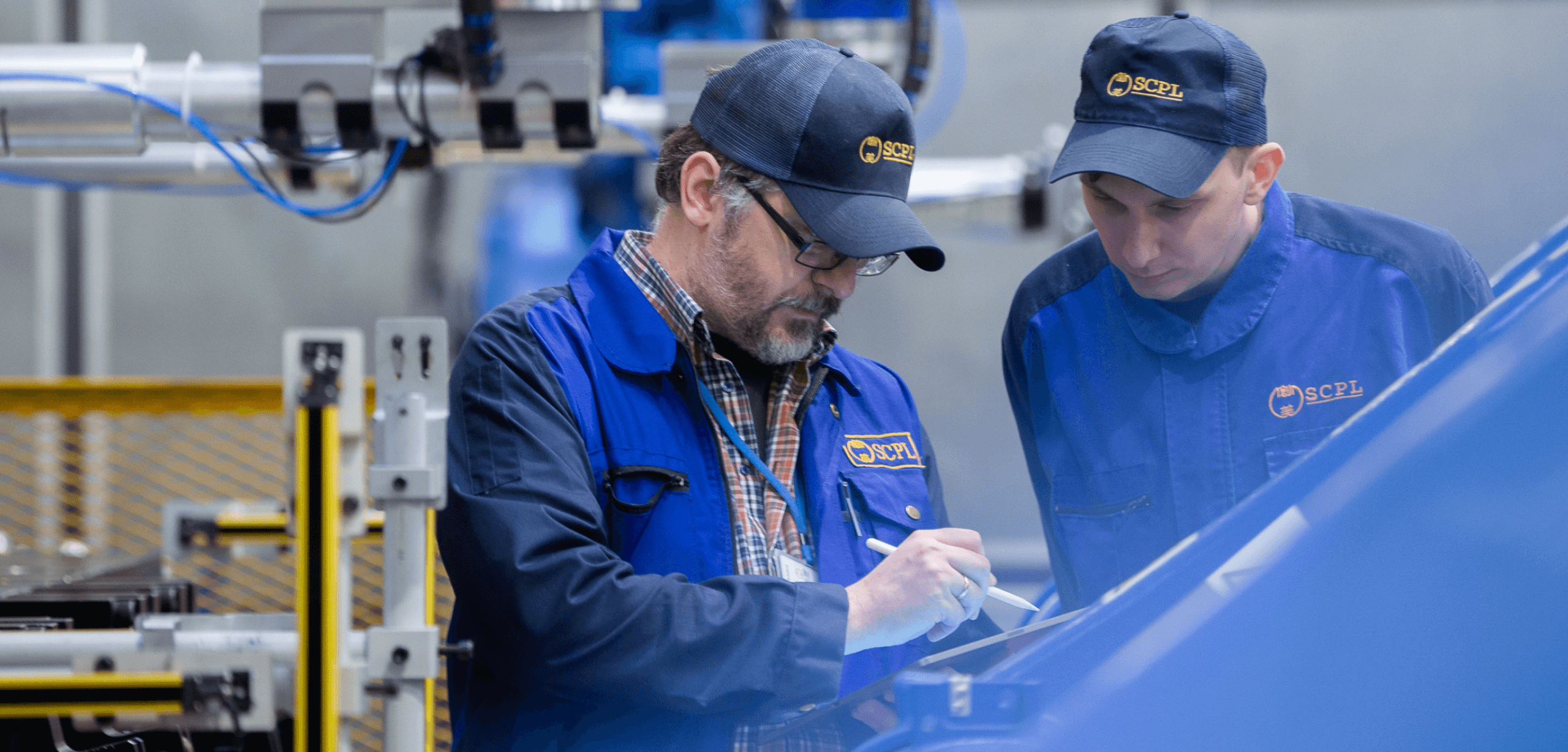
Misalignment isn’t just frustrating—it’s expensive.
And for manufacturers, it shows up everywhere: missed handoffs, production delays, rework. Most of the time, the problem isn’t technical—it’s human. Teams talk past each other, and departments fall out of sync.
As the industry shifts toward a more human-centric model with Industry 5.0, alignment is becoming non-negotiable—not just between managers and operators but across everyone involved in bringing a product to life.
A recent review in Applied Sciences listed communication as one of the most critical factors for driving continuous improvement on the shop floor. The study looked at 60 different influences on team performance and found that clear communication wasn’t just helpful but foundational. When teams can’t share ideas clearly, alignment breaks down, and progress stalls.
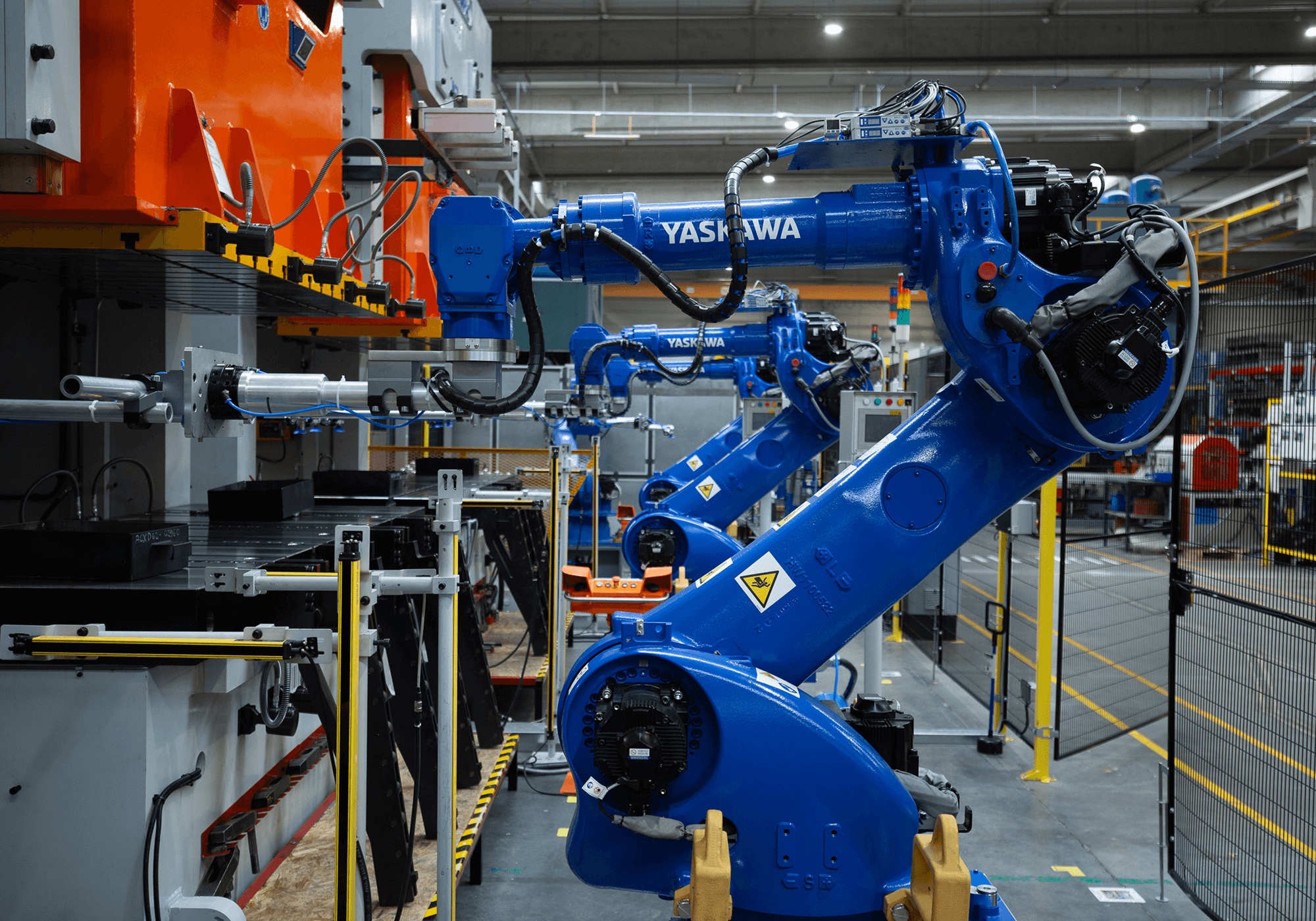
When ideas don’t land, work grinds to a halt
In manufacturing, that breakdown shows up in the smallest moments.
Sketches get misread, details slip through, and feedback gets lost between tools. Every production delay tells the same story: someone misunderstands what someone else meant.
The breakdown isn’t just verbal; it’s visual.
When ideas stay stuck in someone’s head or on a napkin sketch, they don’t scale. Teams rely on hand drawings and verbal instructions to fill in the gaps, but these methods often fall short. Communication in 3D could bridge this gap, making it easier to visualize and share ideas across the team.
And this isn’t just an isolated problem. Whether it’s 3M’s advanced maintenance teams or Sohbi’s process engineers on the factory floor, the communication gap shows up everywhere, regardless of role or tooling.
3M: How the Technical Workshop turned miscommunication into visual collaboration
At 3M’s German workshop, daily delays were the norm. Hand sketches passed through multiple hands—engineers, apprentices, operators—creating room for constant misinterpretation.
“Some people came with hand sketches,” said Marcel, a 3M supervisor. “Then it went to someone else, then an apprentice, then the person at the drill. So many chances to misinterpret the original idea.”
Clarifications dragged on and production slowed, with CAD tools stuck on office desktops and too rigid for quick idea exploration.
Then, Marcel found Shapr3D.
“After watching the tutorial, I got started right away. It was that easy.”
Everyone on the team already had iPads. Suddenly, modeling didn’t have to happen elsewhere; it could happen right where the work did.
“I opened my iPad, joined the Teams meeting, launched Shapr3D, and just started modeling what they were talking about, so we could discuss it while they saw the idea take shape right in front of them. I could explain directly what we could do and what we were capable of. And based on their feedback, I modified the model.”
From there, 3D became the language of collaboration. Visual, fast, and shared.
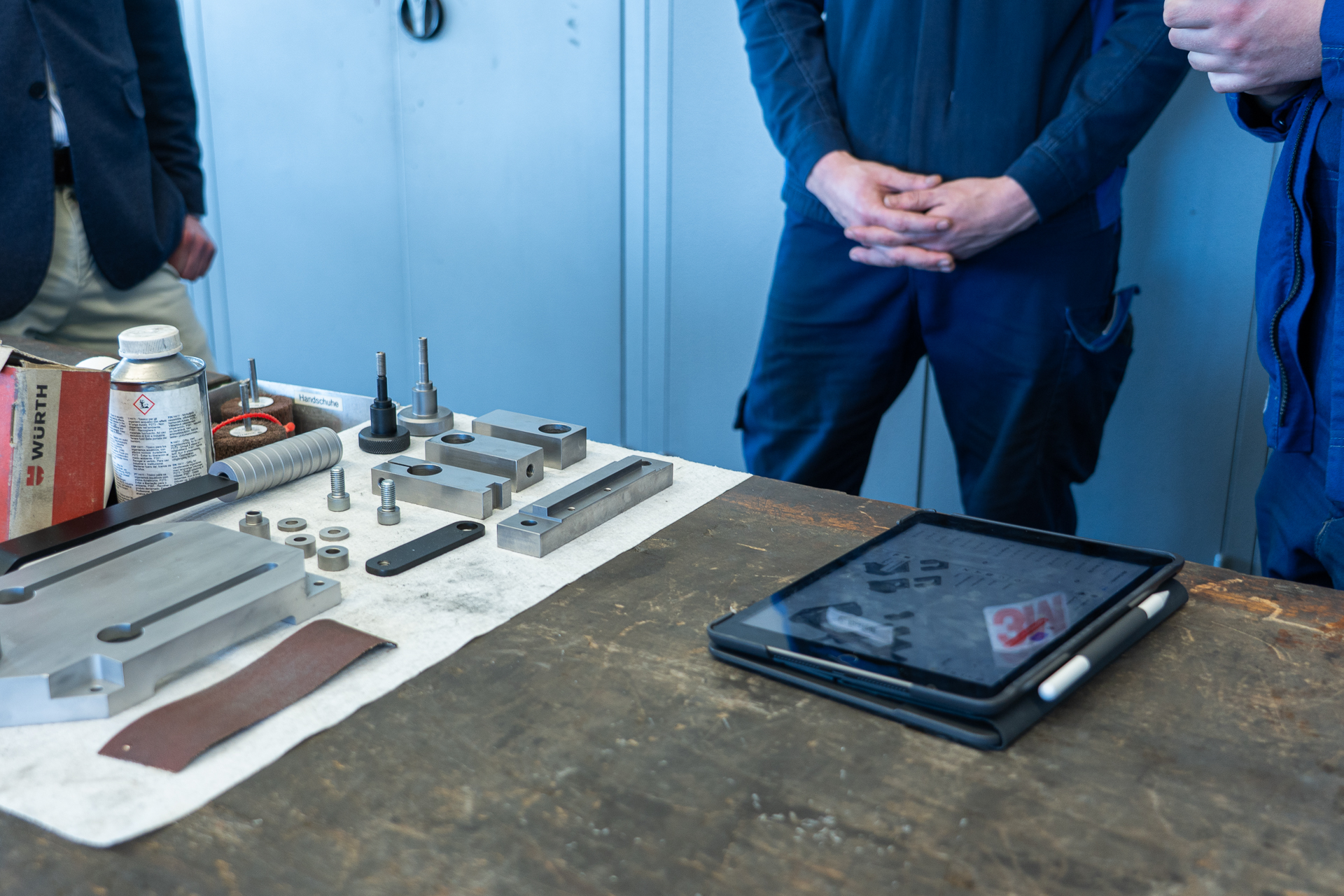
Sohbi Craft: Design was always the bottleneck
In Poland, Sohbi Craft was feeling the pressure. As a manufacturer tasked with developing complex production lines, the product engineering team often found itself slowed down, not by a lack of ideas, but by the planning phase that struggled to keep up. Without the right tools, designs lagged behind real-world needs, and delays stacked up.
“We didn’t design in 3D. We mostly relied on the experience of our engineers. Mistakes happened. And we caught them late.”
— Arkadiusz, Manager of Production Engineering, Sohbi Craft Poland
That meant builds based on assumptions, testing ideas live on the shop floor, waiting for corrections, and hoping errors wouldn’t surface during full production.
Szymon, an industrial robot specialist at Sohbi, described it clearly:
“Before Shapr3D, we had to do a lot of things by eye. Something always turned out to be missing or wrongly selected.”
The bottleneck wasn’t a lack of ideas—it was the dependency. They needed a way to take action without waiting on design teams or CAD training.
Then, they discovered Shapr3D. No formal CAD background? No problem.
“Most of the guys who use it had never touched CAD before. They just started modeling—and found it easy.”
— Marcin, Industrial Engineering Expert, Sohbi Craft
The way ideas were shared changed. Suddenly, the people building the process could show them. Visually, clearly, in 3D.
And for the first time, the people who built the line could design the line.
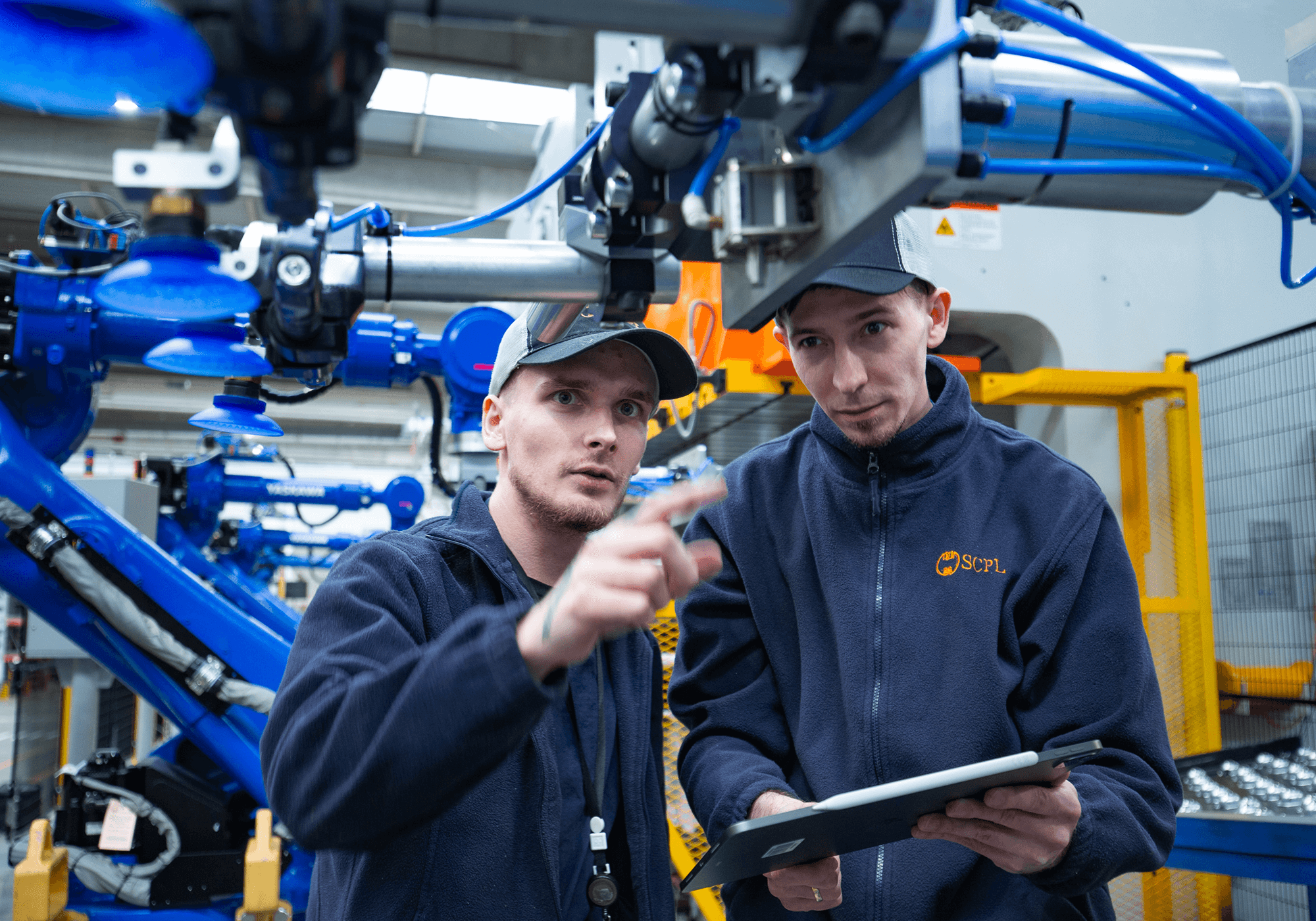
Bringing feedback and design into the same space
Manufacturing teams needed a faster and clearer way to collaborate, without having to bounce between tools or versions. What Google Docs did for writing, Shapr3D does for 3D design.
Shapr3D gives teams a single source of truth, so the model becomes the meeting room, the inbox, and the blueprint.
Once a design is ready for feedback, there's no need to export files or jump through extra hoops. With secure review links, teams can share work-in-progress models with anyone, instantly.
With the collaborator role, even non-CAD users can view, comment on, and provide feedback on high-quality 3D designs across iPad, Mac, Windows, or even Vision Pro—without needing to export or install extra software.
That kind of alignment does more than speed things up. It catalyzes innovation. Ideas sharpen, feedback sticks, and decisions happen in context. That’s synthesized learning. That’s how teams shift from reactive to agile.
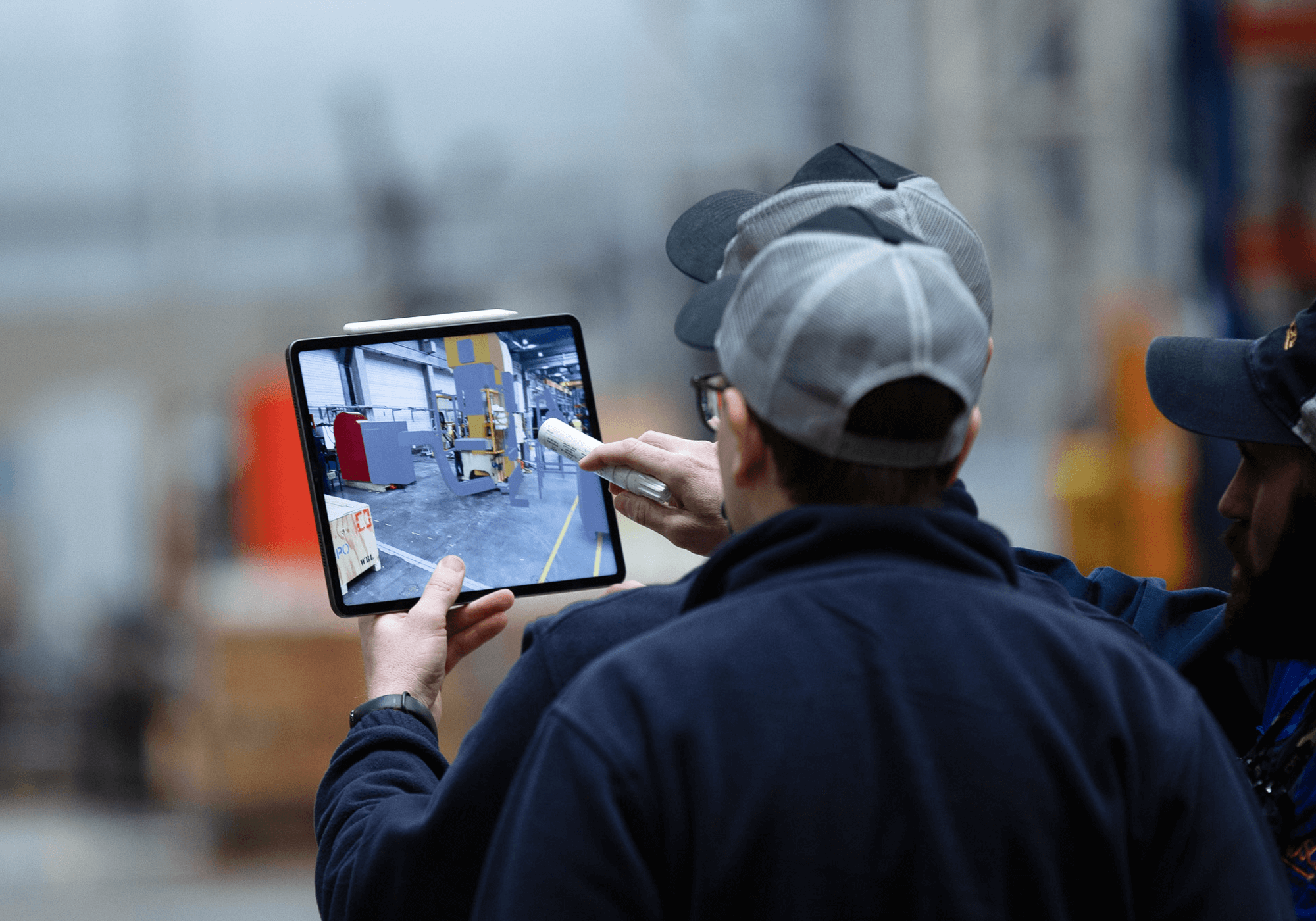
The future of manufacturing starts on the floor
Tools don’t transform teams. Empowerment does.
At 3M and Sohbi, the tool wasn’t the win. The shift was in who owned the design process. They collapsed the distance between idea and action. And they brought design into every part of production.
That’s what agile looks like in the manufacturing world. That’s what happens when communication becomes visual, shared, and instant.
And that’s what Shapr3D was built for.